Stahl ist das heute am häufigsten verwendete Material. Stahl hat jedoch einen großen Nachteil-seine hohe Korrosionsrate. Der Schutz von Stahlkonstruktionen und Bauteilen ist daher von großer wirtschaftlicher Bedeutung.
Der beste Korrosionsschutz für Stahl wird mit Zink erhalten. Zinkbeschichtungen auf Stahl schützen auf zwei Arten vor Korrosion:
- Durch eine Barrierewirkung, d.h. sie verhindern, dass Sauerstoff und Feuchtigkeit an die Stahloberfläche gelangen.,
- Durch kathodischen Schutz bei Kratzern, Spänen, Kanten etc.
Zink ist ein Metall mit relativ geringem galvanischem Potential und hoher Korrosionsneigung. Die Korrosionsrate ist jedoch in den meisten Umgebungen gering, da die Oberfläche der Beschichtung schnell mit Korrosionsprodukten bedeckt ist, die anschließend vor weiterer Korrosion schützen.
Korrosion in der Atmosphäre
Wenn ein feuerverzinktes Objekt das Zinkbad verlässt, wird die Oberfläche des Objekts sofort von Sauerstoff in der Luft angegriffen., Die resultierende Oxidschicht hat sehr wenig Fähigkeit gegen Korrosion zu schützen. Wasser und Kohlendioxid in der Luft verändern jedoch schnell die Oxidschicht zu Zinkcarbonaten. Diese ergeben eine versiegelte Schicht mit sehr guter Haftung. Da die Carbonate eine sehr geringe Wasserlöslichkeit aufweisen, bieten sie einen hervorragenden Schutz der Oberfläche der Zinkbeschichtung. Die ursprüngliche glänzende Oberfläche mit metallischem Glanz verschwindet und wird durch eine matte, hellgraue Farbe ersetzt (Abb.1).
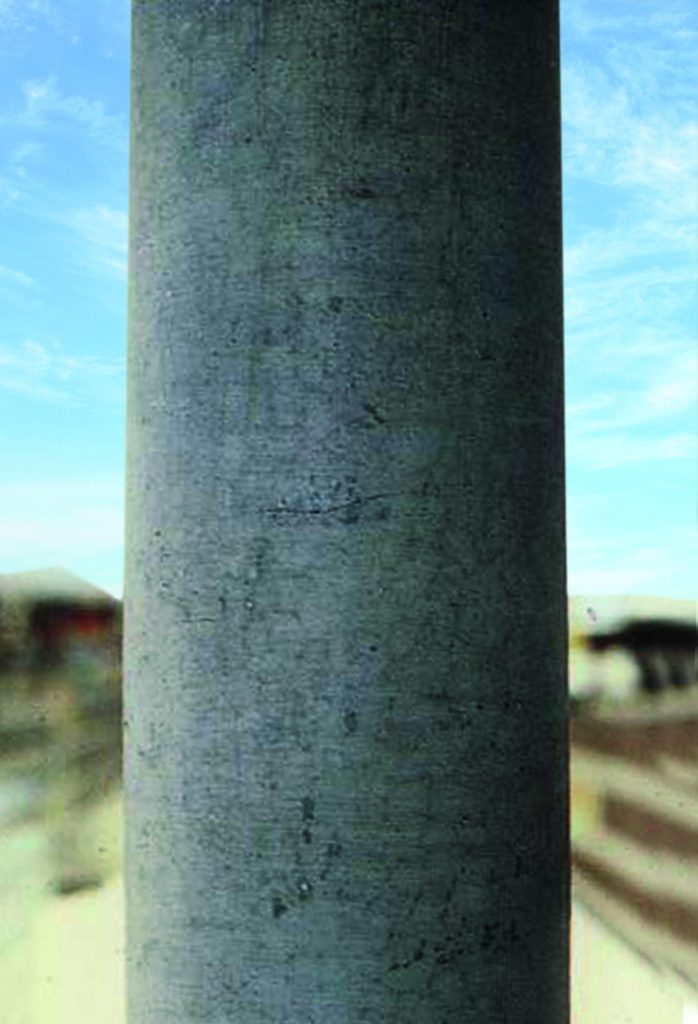
Abb 1., Freiliegende Oberfläche einer Zinkbeschichtung mit äußerer Schicht aus reinem Zink. Die glänzende Oberfläche verschwindet, um durch graue Korrosionsprodukte (manchmal Zinkpatina genannt) ersetzt zu werden.
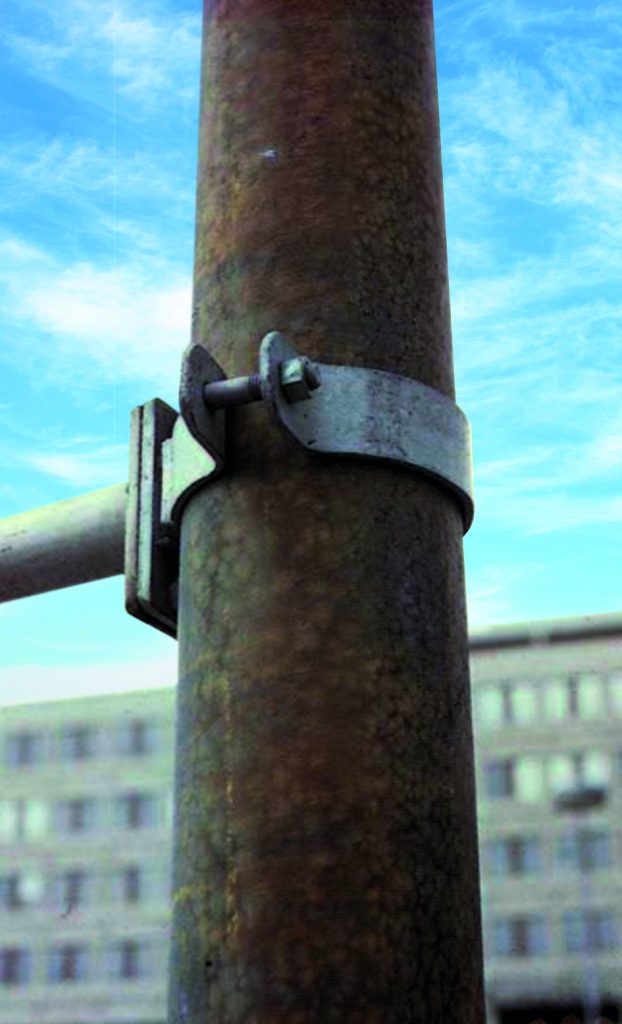
Abb. 2. Verfärbte Oberfläche auf Beleuchtungssäule. Die Beschichtung besteht hauptsächlich aus einer Eisen-Zink-Legierung, die sich bis zur Oberfläche erstreckt. Eisen wird während der Korrosion ausgesetzt, was zur Rostbildung führt. Es ist nur Oberflächenrost und nur von ästhetischer Bedeutung.,
Außenluft enthält mehr oder weniger korrosive Elemente-Gase, Ruß, Feuchtigkeit (Nebel, Tau, Regen, Schnee), inerten und aggressiven Staub. Die Levels können je nach Standort und Jahreszeit variieren. Sulfate und Sulfite von Zink sind wasserlöslich und haften schlecht an der Zinkoberfläche. Sie werden daher leicht durch Regen weggespült. Eine frische Zinkoberfläche wird dann einem Angriff durch Sauerstoff in der Luft ausgesetzt und der Korrosionszyklus wird wiederholt. Die Korrosion in schwefeloxidhaltiger Luft ist daher größer als in sauberer Luft., Die Menge an Schwefeldioxid in der Atmosphäre hat in den letzten Jahren jedoch drastisch abgenommen, und folglich hat auch die Zinkkorrosion abgenommen.
In marinen Umgebungen wird die Korrosion von Zink durch den Salzgehalt der Luft beeinflusst. Meeresluft enthält jedoch geringe Mengen Magnesiumsalze mit guten passivierenden Einflüssen. Die Korrosion ist daher nicht so groß wie erwartet. Der Salzgehalt der Luft reduziert sich schnell von der Küste weg.
Die Korrosion von Zink wird von vielen Faktoren beeinflusst., Dies bedeutet, dass keine allgemein anwendbare Formel für Korrosionsraten angegeben werden kann. Zinkbeschichtungen werden jedoch seit langem unter einer Vielzahl von Bedingungen verwendet, um Stahl vor Rost zu schützen. Eine große Anzahl von Langzeittests wurde ebenfalls durchgeführt. Kenntnisse über die Korrosion von Zink und Korrosionsraten in verschiedenen Umgebungen sind daher gut. Heute gibt es Beispiele für Zinkbeschichtungen, die seit mehr als hundert Jahren ausgesetzt sind.
Die Farbe der Korrosionsprodukte variiert je nach Umgebung, in der sie gebildet werden., Meeresumgebungen ergeben im Vergleich zu ländlichen und städtischen Umgebungen etwas weißere Korrosionsprodukte. Korrosionsprodukte sind in städtischen Umgebungen normalerweise am dunkelsten.
Korrosion in Flüssigkeiten
Die Zinkoberfläche ist beim Eintauchen in eine Flüssigkeit im Allgemeinen mit einer Schutzschicht aus Korrosionsprodukten bedeckt. Flüssigkeiten können jedoch sauer oder alkalisch sein und gelöste oder feste Partikel aggressiver Substanzen enthalten. Die Temperatur und Durchflussrate der Flüssigkeit sind ebenfalls von Bedeutung., All dies bedeutet, dass die Schutzschicht eine stark unterschiedliche Zusammensetzung haben kann oder sich überhaupt nicht bildet.
Elektrochemische Korrosion, die in der Luft eine untergeordnete Rolle spielt, ist in Flüssigkeiten von größerer Bedeutung. Das Ausmaß der elektrochemischen Korrosion hängt von der elektrischen Leitfähigkeit der Flüssigkeit ab, die den Schutzeinfluss der Zinkschicht über größere oder kleinere Bereiche beeinflusst.
Der pH-Wert der Flüssigkeit ist von größter Bedeutung. Die Korrosionsrate von Zink ist normalerweise niedrig und stabil im pH-Bereich von 5,5-12,5 bei Temperaturen zwischen 0 und 20 °C., Korrosion außerhalb dieses Bereichs ist in der Regel schneller.
Hartes Wasser, das Kalk und Magnesium enthält, ist weniger aggressiv als weiches Wasser. Zusammen mit Kohlendioxid bilden diese Substanzen auf der Zinkoberfläche sparsam lösliche Carbonate, die das Zink vor weiterer Korrosion schützen.
Weiches Wasser greift häufig Zink an, da durch das Fehlen von Salzen die Schutzschicht nicht gebildet werden kann.
Aggressive Weichgewässer finden sich in vielen Flüssen und Seen in Finnland, Norwegen, Schweden und ähnlichen Umgebungen.
Wenn der Durchfluss größer als 0 ist.,5 m / s Die Bildung der Schutzschicht auf der Zinkoberfläche wird gehemmt und die Korrosion beschleunigt.
Die Wassertemperatur ist von großer Bedeutung für die Korrosionsrate. Über etwa 55 °C erhalten die schichtbildenden Korrosionsprodukte eine grobkörnige Struktur und verlieren die Haftung an der Zinkoberfläche. Sie lassen sich leicht entfernen und setzen neues, frisches Zink für einen anhaltenden und schnellen Korrosionsangriff frei. Die Korrosionsrate erreicht bei etwa 70 °C ein Maximum, wonach sie abnimmt, so dass sie bei 100 °C etwa gleich ist wie bei 50 °C.,
Die Korrosionssequenz in Wasser ist sehr komplex und wird stark durch sehr geringe Schwankungen in der Zusammensetzung des Wassers beeinflusst. Es ist daher schwierig, allgemein anwendbare Regeln festzulegen. Das Informaton in Abbildung 3 basiert auf praktischen Erfahrungen und enthält Richtlinien für verschiedene Wasserarten.
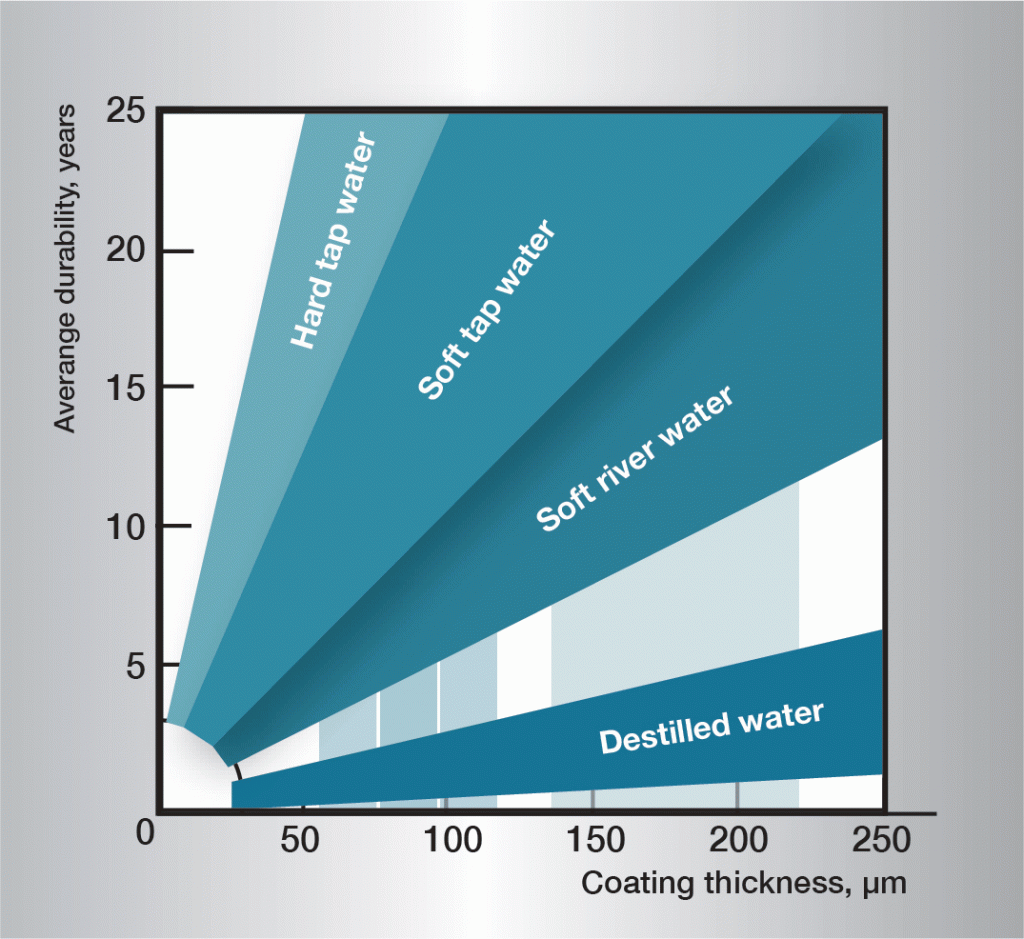
Abb. 3. Lebensdauer in verschiedenen Gewässern.,
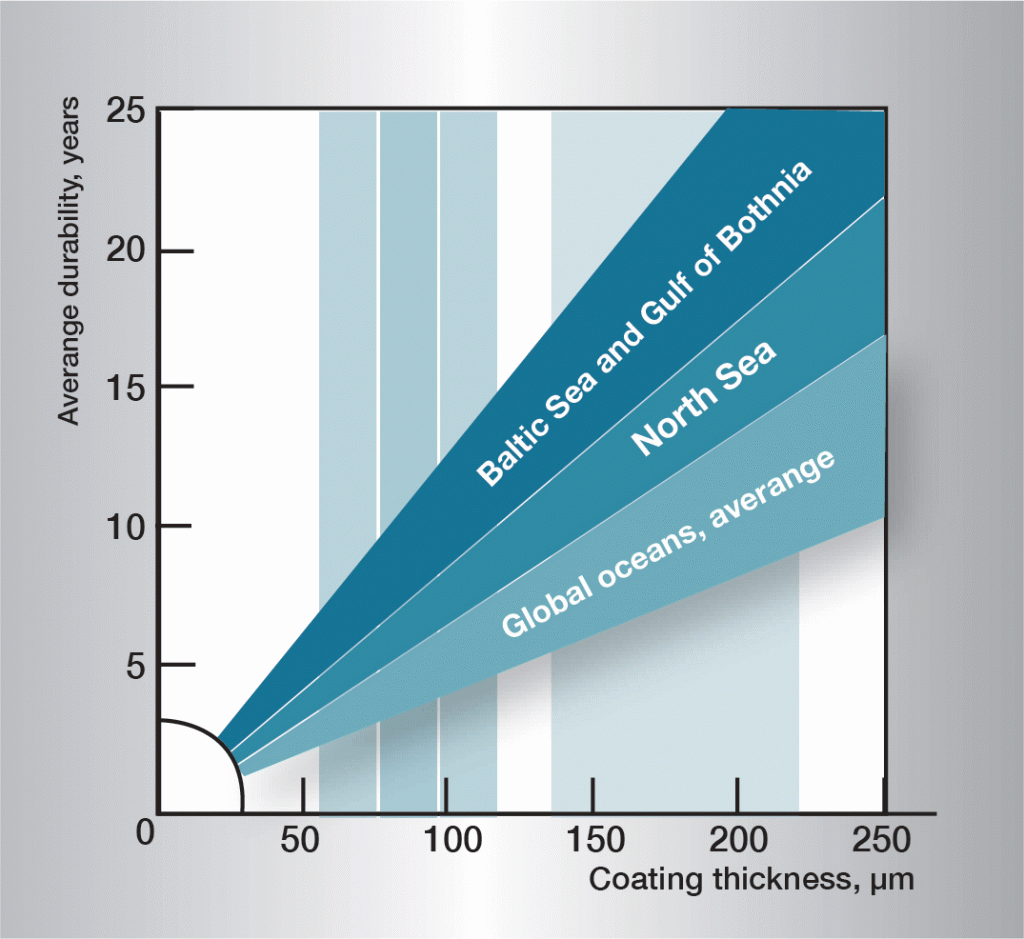
Nasslagerfleck
Manchmal erscheint auf verzinkten Oberflächen eine weiße, mehlige und voluminöse Schicht, die als Nasslagerfleck oder weißer Rost bezeichnet wird (Abb.4). Weißrost bildet sich auf Materialien mit neu verzinkten, glänzenden Oberflächen und insbesondere in Spalten zwischen dicht gepackten Blechen, Winkeleisen und ähnlichen Materialien. Voraussetzung ist, dass das Material unter Bedingungen, bei denen die Feuchtigkeit nicht schnell verdunsten kann, Kondensations-oder Regenwasser ausgesetzt ist., Zinkoberflächen, die bereits eine normale Schutzschicht aus Korrosionsprodukten erhalten haben, werden selten angegriffen. Wenn Zinkbeschichtungen Luft ausgesetzt werden, bilden sich Zinkoxid und Zinkhydroxid. Unter dem Einfluss von Kohlendioxid in der Luft werden diese in basische Zinkcarbonate umgewandelt. Wenn der Luftzutritt zur Zinkoberfläche wie in engen Spalten eingeschränkt ist, erhält der Bereich unzureichendes Kohlendioxid, um die Bildung der normalen kohlensäurehaltigen Schicht zu ermöglichen.
Die Nasslagerfleckschicht ist voluminös und porös und nur lose an der Zinkoberfläche befestigt., Infolgedessen besteht kein Schutz vor fortgesetztem Angriff. Korrosion kann daher so lange anhalten, wie Feuchtigkeit auf den Oberflächen verbleibt. Wenn ein Nasslagerfleck aufgetreten ist, sollte das Objekt gestapelt werden, damit die Oberflächen schnell trocknen können. Dies stoppt den Angriff und bei freiem Zugang zu Luft bildet sich die normale Schutzschicht. Der Nasslagerfleck wird allmählich abgewaschen und die Beschichtung erhält ein Aussehen, das für freiliegenden, feuerverzinkten Stahl normal ist.,
Da dieses weiße Korrosionsprodukt sehr sperrig ist (etwa das 500-fache des Zinks, aus dem es gebildet wurde), kann es ernst erscheinen. Nasslagerflecken haben jedoch oft wenig oder gar keine Bedeutung für die Lebensdauer des Korrosionsschutzes. Bei sehr dünnen Beschichtungen, z.B. auf galvanisierten Gegenständen, kann jedoch ein starker Anfall von Nassspeicherfleck von Bedeutung sein.
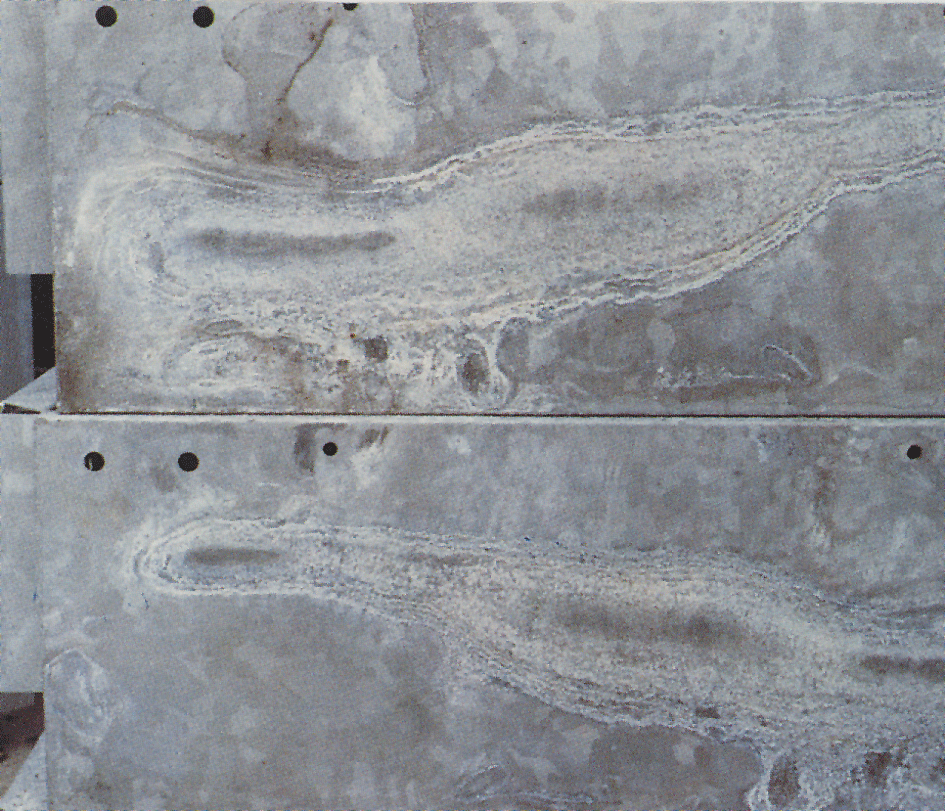
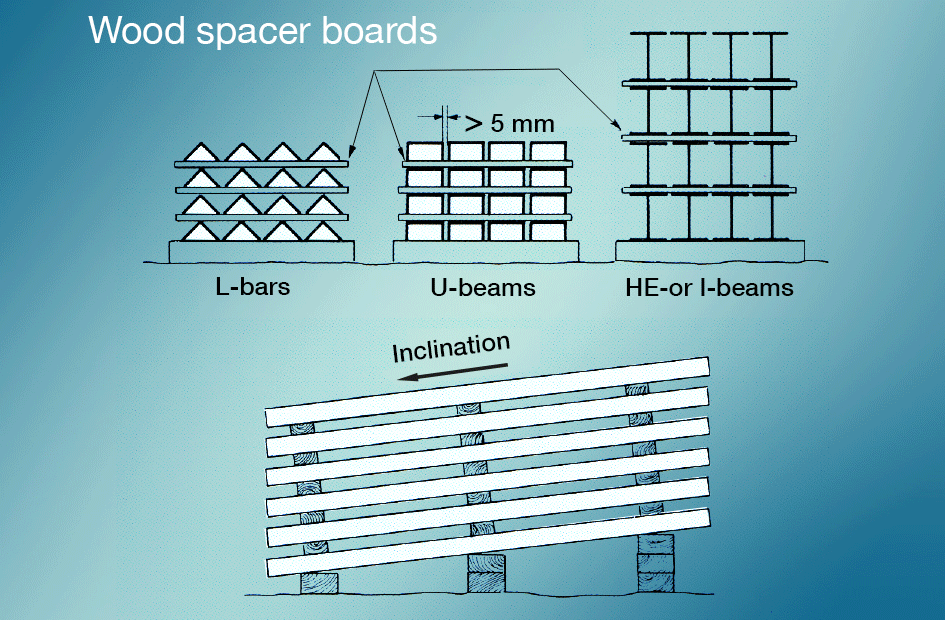
Nasslagerflecken werden am besten vermieden, indem verhindert wird, dass neu verzinkte Oberflächen während des Transports mit Regen oder Kondensat in Kontakt kommen., Im Freien gelagerte Materialien sollten gestapelt werden, damit das Wasser leicht abfließen kann und alle Oberflächen gut belüftet sind (Abb. 5). Das Lackieren nach dem Verzinken bietet einen sehr guten Schutz.
Korrosion im Boden
Die Korrosionsbedingungen im Boden sind sehr kompliziert und Variationen können zwischen verschiedenen Orten, auch in unmittelbarer Nähe zueinander, groß sein. Der Boden kann verwitterte Produkte, freie oder gebundene Salze, Säuren und Laugen, Mischungen organischer Substanzen, oxidierende oder reduzierende Pilze, Mikroorganismen usw. enthalten., Abhängig von seiner Struktur hat der Boden unterschiedliche Durchlässigkeit für Luft und Feuchtigkeit. Normalerweise ist der Sauerstoffgehalt geringer als in Luft, während der Kohlendioxidgehalt höher ist.
Schwedische Böden sind im Allgemeinen nicht sehr aggressiv. Durchschnittliche Korrosion für Zink wird in der Regel als 5 µm pro Jahr genommen. Stark aggressive Böden sind selten zu sehen. In Nord-und West Bothnien können Böden Schwefel enthalten. Sie sind oft schwarz, aber heller, wenn sie Luft ausgesetzt werden. In diesen Böden sind die Zinkkorrosionsraten sehr hoch.
Eine Methode zur Bestimmung der Korrosivität eines Bodens ist die Messung seiner Widerstandsfähigkeit., Wenn die Bodenresistenz nicht bestimmt werden kann, können die in Abbildung 6 aufgeführten Faustregeln als Richtschnur dienen. In Bezug auf die Exposition von Metallen gegenüber Böden ist es jedoch ratsam, sich von entsprechend qualifizierten Quellen fachkundig beraten zu lassen.
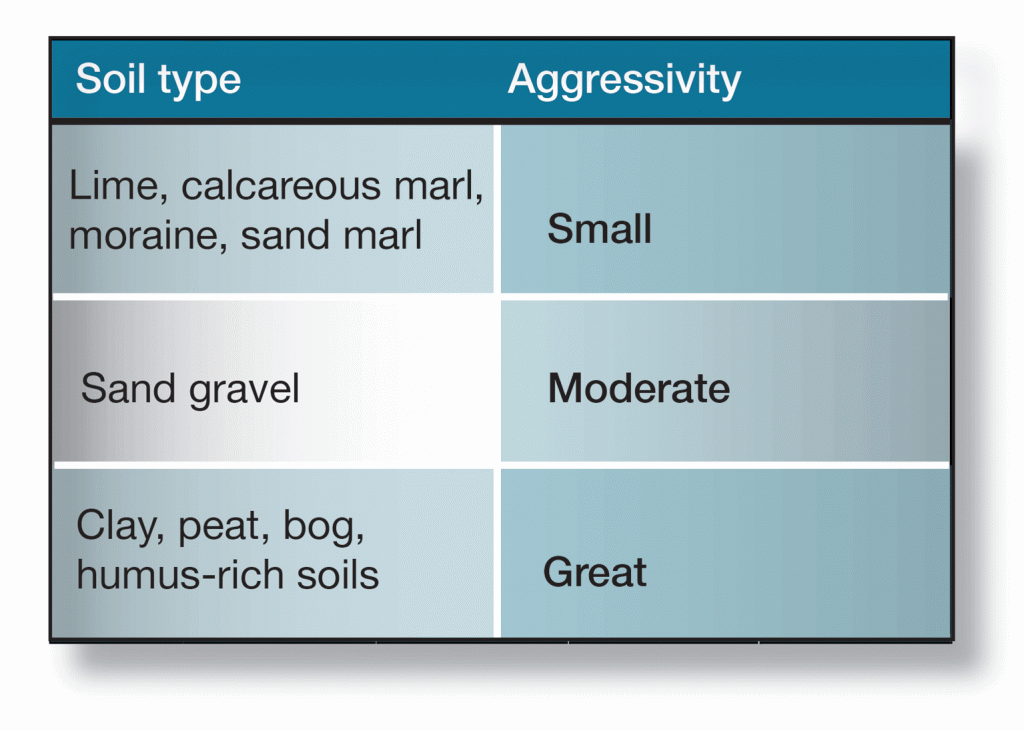
Galvanische Korrosion
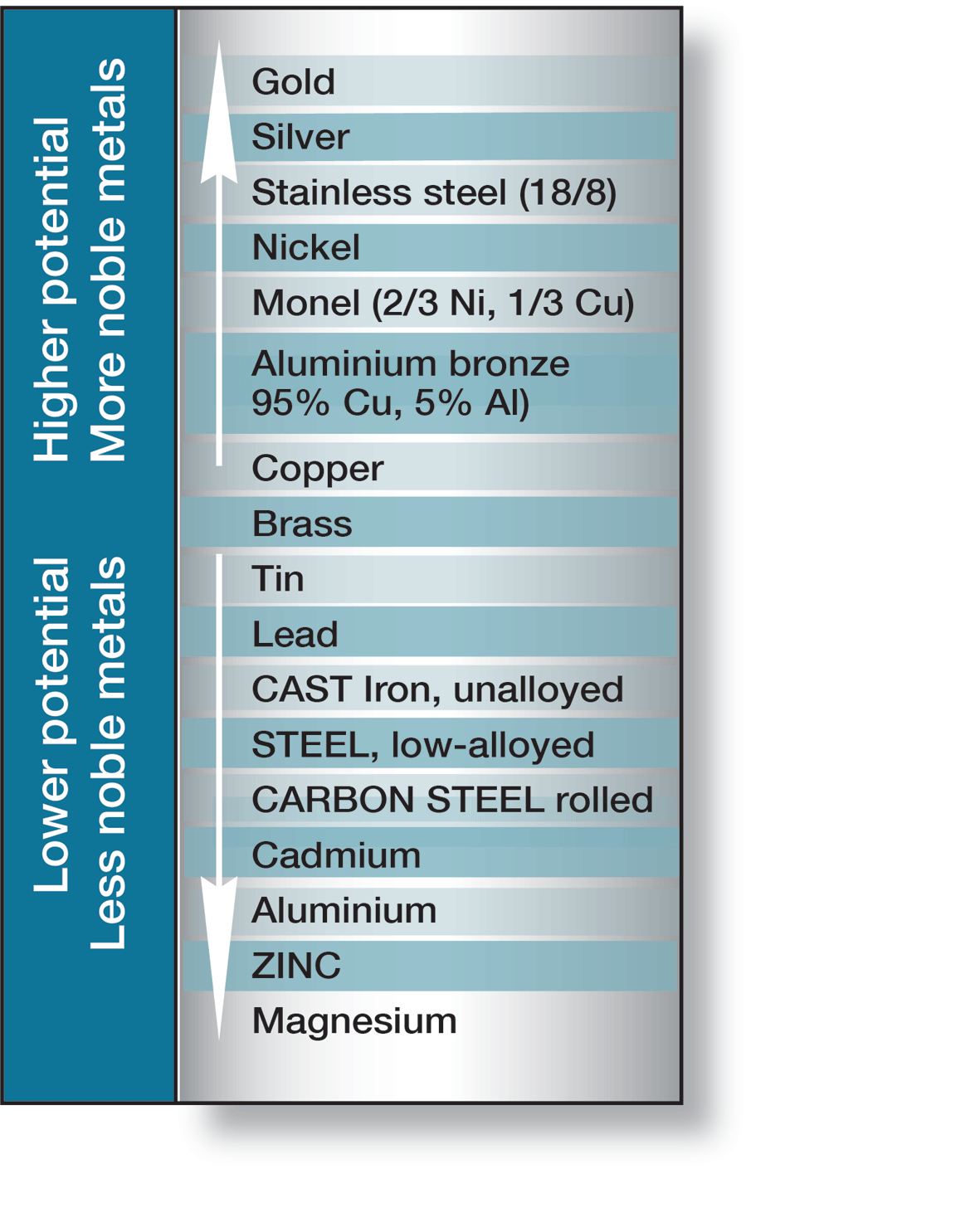
Wenn zwei verschiedene Metalle oder Legierungen, ganz oder teilweise von einem Elektrolyten umgeben, miteinander verbunden sind, entsteht eine galvanische Zelle. Welches Metall die Anode oder Kathode wird, wird durch ihre Elektrodenpotentiale in dem betreffenden Elektrolyten bestimmt. Im Meerwasser, das den meisten praktischen Bedingungen entspricht, nehmen einige Metalle und Legierungen unterschiedliche Positionen auf der elektrochemischen Skala ein, wie in Abbildung 7 gezeigt.,
Wenn Stahl mit Kupfer oder Messing verbunden ist, wird der Stahl zur Anode in der Zelle und korrodiert. Wenn jedoch Stahl mit Cadmium, Aluminium, Zink oder Magnesium verbunden ist, wird er zur Kathode und ist vor Korrosion geschützt, während das Anodenmetall verbraucht wird. Galvanische Korrosion wird auch Bimetallkorrosion genannt und wird verwendet, um Unterwasserstrukturen vor Korrosion zu schützen, wenn sie als kathodischer Schutz bezeichnet wird.
Kathodischer Schutz durch Zinkbeschichtungen
In feuerverzinktem Stahl stehen Zink und Stahl in gutem elektrischen Kontakt miteinander., Wenn die Zinkbeschichtung in Gegenwart eines Elektrolyten beschädigt ist, wird eine galvanische Zelle erzeugt. Der Elektrolyt könnte Kondensat oder Regenwasser sein. Manchmal kann die gesamte Struktur in Flüssigkeit getaucht werden. In dieser Zelle wird das Zink zur Anode oder zum Auflösungspol, der freiliegende Stahl wird zur Kathode und ist daher vor Korrosion geschützt.
In der Anfangsphase ist es oft möglich, eine schwache UST-Bildung auf dem freiliegenden Teil der Stahloberfläche zu sehen, wo die Beschichtung beschädigt wurde, aber nach einer Weile bilden sich weißlich-graue Bereiche, die sich allmählich über die gesamte beschädigte Stelle ausbreiten., Die Zinkbeschichtung korrodiert und sparsam lösliche Zinklegierungen steigen auf die Kathodenoberfläche ab, wo sie den Stahl vor fortgesetztem Rostangriff schützen. Dies wird oft als „Selbstheilung“ bezeichnet, was eine falsche Bezeichnung ist, da die Zinkschicht natürlich nicht wiederhergestellt wird.
Aufgrund des kathodischen Schutzes, der durch das Zink erzeugt wird, kann Rost nicht an der Stelle der Beschädigung unter die Beschichtung „kriechen“, so dass er unter Farbfilmen oder Beschichtungen von Metallen kriechen kann edler als Stahl., Zinkbeschichtungen auf Stahl sind ungewöhnlich, da ein ziemlich großer Bereich der Beschädigung der Beschichtung keinen katastrophalen Rostschutzverlust verursacht. Der Bereich des kathodischen Schutzes hängt von der Art des Elektrolyten ab, der die Zelle erzeugt. Bei Strukturen in normaler Atmosphäre ist es üblich, eine Schutzwirkung über mehrere Millimeter zu erwarten. Im Meerwasser sind jedoch deutlich größere Entfernungen zu erwarten.
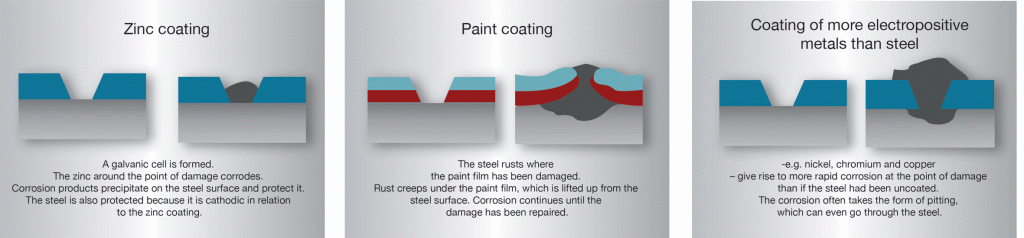
Zinkbeschichtungen in Kontakt mit Nichteisenmetallen
Die elektrochemische Potentialskala zeigt, dass Zink weniger edel ist als die gängigsten Metalle. Dies bedeutet, dass, wenn Zink mit diesen Metallen in einer galvanischen Zelle verbunden ist, es das Zink ist, das zum Auflösungspol wird. Grundsätzlich sollten daher solche Verbindungen nach Möglichkeit vermieden werden. Eine gute Methode ist die Verwendung eines Isolators wie Kunststoff oder Gummi am Gelenk.,
Aluminium und Edelstahl können oft direkt an verzinktes Material in Luft oder ziemlich trockenen Umgebungen angeschlossen werden, ohne dass eine merkliche Korrosion auftritt. In Wasser sollte jedoch immer ein Isolator verwendet werden.
Kupfer und Kupferlegierungen sind elektrisch aktiver und es kommt häufig zu einer Freisetzung von Kupferionen, die sich über große Flächen ausbreiten und einen spürbaren Angriff verursachen. Aus diesem Grund sollten diese Metalle niemals mit verzinktem Stahl in Berührung kommen dürfen und ein Isolator sollte verwendet werden.,
Feuerverzinkter Stahl in Kontakt mit Mörtel, Putz und Holz
Feuchter Mörtel und Putz greifen Zink an. Der Angriff hört auf, wenn das Material austrocknet. Trockenes oder mäßig feuchtes Holz, sowohl imprägniert als auch unvorbereitet, kann mit feuerverzinkten Nägeln gut genagelt werden. Bei Nägeln oder Gewindeverbindungen, die ständig Wasser ausgesetzt sind, wird jedoch ein säurebeständiges Material bevorzugt. Andere trockene Baumaterialien wie Mineralwolle greifen Zink nicht an.,
Verpackung und Transport von verzinktem Stahl
Obwohl eine feuerverzinkte Beschichtung einer ziemlich groben Behandlung standhalten kann, sollte sie während der Lagerung und des Transports vorsichtig gehandhabt werden. Bei langen Gütern schützt die einfache Verpackung und Bindung in Bündel nicht nur vor mechanischen Beschädigungen, sondern erleichtert oft auch den Transport selbst. Das Verpacken und Binden sollte jedoch so erfolgen, dass die Gefahr einer Nasslagerbelastung vermieden wird. Abstandshalter sollten verwendet werden, um solche Angriffe zu verhindern.