l’acier est le matériau le plus couramment utilisé aujourd’hui. Cependant, l’acier a un gros inconvénient-son taux de corrosion élevé. La protection des structures et des composants en acier est donc d’une grande importance économique.
la meilleure protection contre la corrosion de l’acier est obtenue avec du zinc. Les revêtements de Zinc sur l’acier protègent contre la corrosion de deux manières:
- par un effet barrière, c’est-à-dire qu’ils empêchent l’oxygène et l’humidité d’atteindre la surface de l’acier.,
- En donnant une protection cathodique aux rayures, aux copeaux, aux bords, etc.
Le Zinc est un métal avec un potentiel galvanique relativement faible et une tendance élevée à la corrosion. Cependant, le taux de corrosion est faible dans la plupart des environnements, car la surface du revêtement est rapidement recouverte de produits de corrosion, qui protègent ensuite contre une corrosion supplémentaire.
Corrosion dans l’atmosphère
Lorsqu’un objet galvanisé à chaud quitte le bain de zinc, la surface de l’objet est immédiatement attaquée par l’oxygène dans l’air., La couche d’oxyde résultante a très peu de capacité à protéger contre la corrosion. Cependant, l’eau et le dioxyde de carbone dans l’air changent rapidement la couche d’oxyde en carbonates de zinc. Ceux-ci donnent une couche scellée avec une très bonne adhérence. Étant donné que les carbonates ont une très faible solubilité dans l’eau, ils offrent une excellente protection à la surface du revêtement de zinc. La surface brillante d’origine avec un lustre métallique disparaît pour être remplacée par une couleur Gris Clair Mat (fig.1).
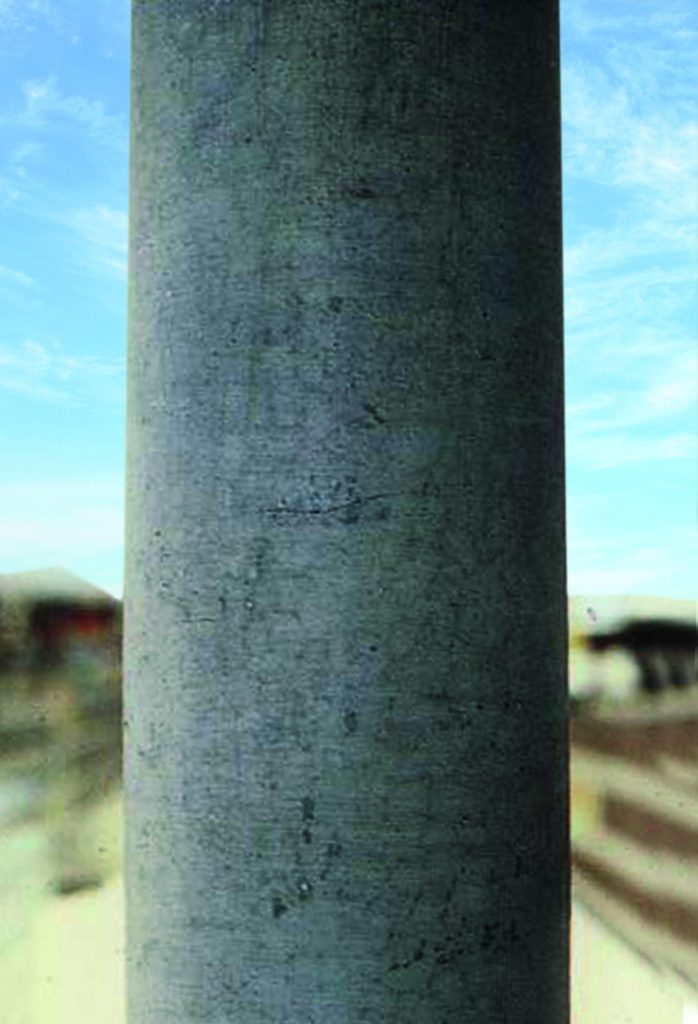
la figure 1., Surface exposée d’un revêtement de zinc avec une couche externe de zinc pur. La surface brillante disparaît pour être remplacée par des produits de corrosion gris (parfois appelés patine de zinc).
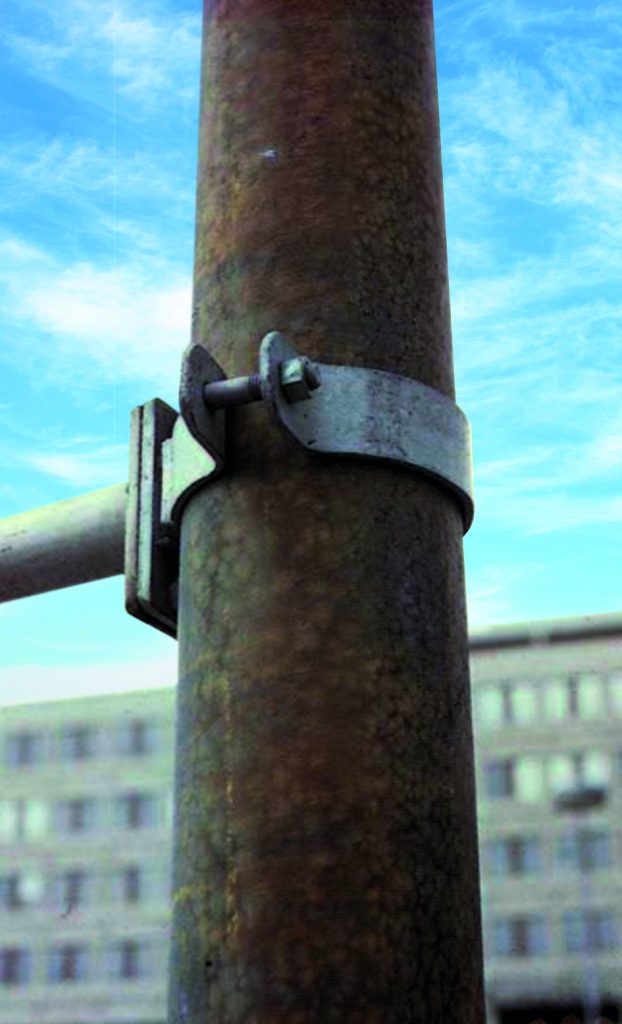
Fig. 2. Surface décolorée sur la colonne d’éclairage. Le revêtement se compose principalement d’un alliage fer-zinc qui s’étend à la surface. Le fer est exposé pendant la corrosion, ce qui conduit à la formation de rouille. Ce n’est que de la rouille de surface et n’a qu’une signification esthétique.,
l’air extérieur contient plus ou moins d’éléments corrosifs — gaz, suie, humidité (brouillard, rosée, pluie, neige), poussière inerte et agressive. Les niveaux peuvent varier en fonction du lieu et de la période de l’année. Les sulfates et les sulfites de zinc sont solubles dans l’eau et ont une mauvaise adhérence à la surface du zinc. Ils sont donc facilement emportés par la pluie. Une surface de zinc frais est alors exposée à l’attaque par l’oxygène dans l’air et le cycle de corrosion est répété. La Corrosion dans l’air contenant des oxydes de soufre est donc plus importante que dans l’air pur., Cependant, la quantité de dioxyde de soufre dans l’atmosphère a considérablement diminué au cours des dernières années et, par conséquent, la corrosion du zinc a également diminué.
en milieu marin, la corrosion du zinc est influencée par la teneur en sel de l’air. Cependant, l’air marin contient de petites quantités de sels de magnésium, avec de bonnes influences passivantes. La Corrosion n’est donc pas aussi importante que ce à quoi on pourrait s’attendre. La teneur en sel de l’air diminue rapidement loin de la côte.
La corrosion du zinc est influencée par de nombreux facteurs., Cela signifie qu’une formule généralement applicable pour les taux de corrosion ne peut pas être donnée. Les revêtements de Zinc sont cependant utilisés depuis longtemps, dans un large éventail de conditions, pour protéger l’acier de la rouille. Un grand nombre de tests à long terme ont également été effectués. La connaissance de la corrosion du zinc et des taux de corrosion dans différents environnements est donc bonne. Aujourd’hui, il existe des exemples de revêtements de zinc exposés depuis plus de Cent Ans.
La couleur des produits de corrosion varie selon l’environnement dans lequel ils sont formés., Les environnements marins donnent des produits de corrosion un peu plus blancs par rapport aux environnements ruraux et urbains. Les produits de Corrosion sont généralement les plus sombres dans les environnements urbains.
Corrosion dans les liquides
la surface du zinc est généralement recouverte d’une couche protectrice de produits de corrosion lorsqu’elle est immergée dans un liquide. Cependant, les liquides peuvent être acides ou alcalins et peuvent contenir des particules dissoutes ou solides de substances agressives. La température et le débit du liquide sont également importants., Tout cela signifie que la couche protectrice peut avoir une composition très variable ou peut ne pas se former du tout.
la corrosion électrochimique, qui joue un rôle secondaire dans l’air, est plus importante dans les liquides. L’étendue de la corrosion électrochimique dépend de la conductivité électrique du liquide, ce qui affecte l’influence protectrice de la couche de zinc sur des zones plus ou moins grandes.
la valeur du pH du liquide est la plus importante. Le taux de corrosion du zinc est normalement faible et stable dans la plage de pH de 5,5-12,5, à des températures comprises entre 0 et 20 °C., La Corrosion en dehors de cette plage est généralement plus rapide.
l’eau dure, qui contient de la chaux et du magnésium, est moins agressive que l’eau douce. Avec le dioxyde de carbone, ces substances forment des carbonates peu solubles à la surface du zinc, protégeant le zinc contre toute corrosion supplémentaire.
l’eau Douce attaque souvent le zinc, car l’absence de sels signifie que la couche protectrice ne peut pas être formée.
on trouve des eaux douces agressives dans de nombreuses rivières et lacs en Finlande, en Norvège, en Suède et dans des environnements similaires.
Si le débit est supérieur à 0.,5 m / s la formation de la couche protectrice sur la surface du zinc est inhibée et la corrosion s’accélère.
la température de l’Eau est d’une grande importance pour le taux de corrosion. Au-dessus d’environ 55 °C, Les produits de corrosion formant des couches acquièrent une structure à gros grains et perdent leur adhérence à la surface du zinc. Ils sont facilement délogés et exposent du zinc neuf et frais pour une attaque de corrosion continue et rapide. Le taux de corrosion atteint un maximum à environ 70 °C, après quoi il diminue de sorte Qu’à 100 °C, il est à peu près le même qu’à 50 °C.,
la séquence de corrosion dans l’eau est très complexe et est fortement influencée par de très petites variations dans la composition de l’eau. Il est donc difficile de donner des règles généralement applicables. L’information de la figure 3 est basée sur l’expérience pratique et donne des lignes directrices pour différents types d’eau.
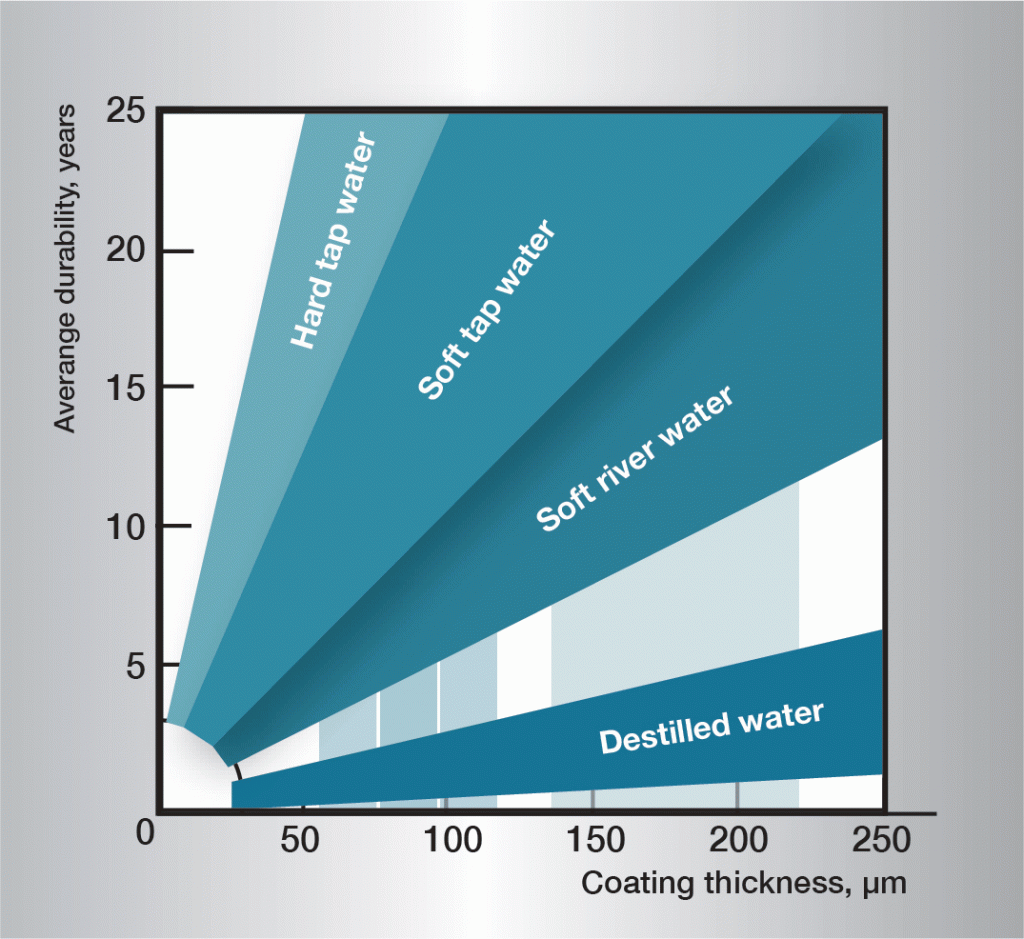
Fig. 3. Durée de vie dans différentes eaux.,
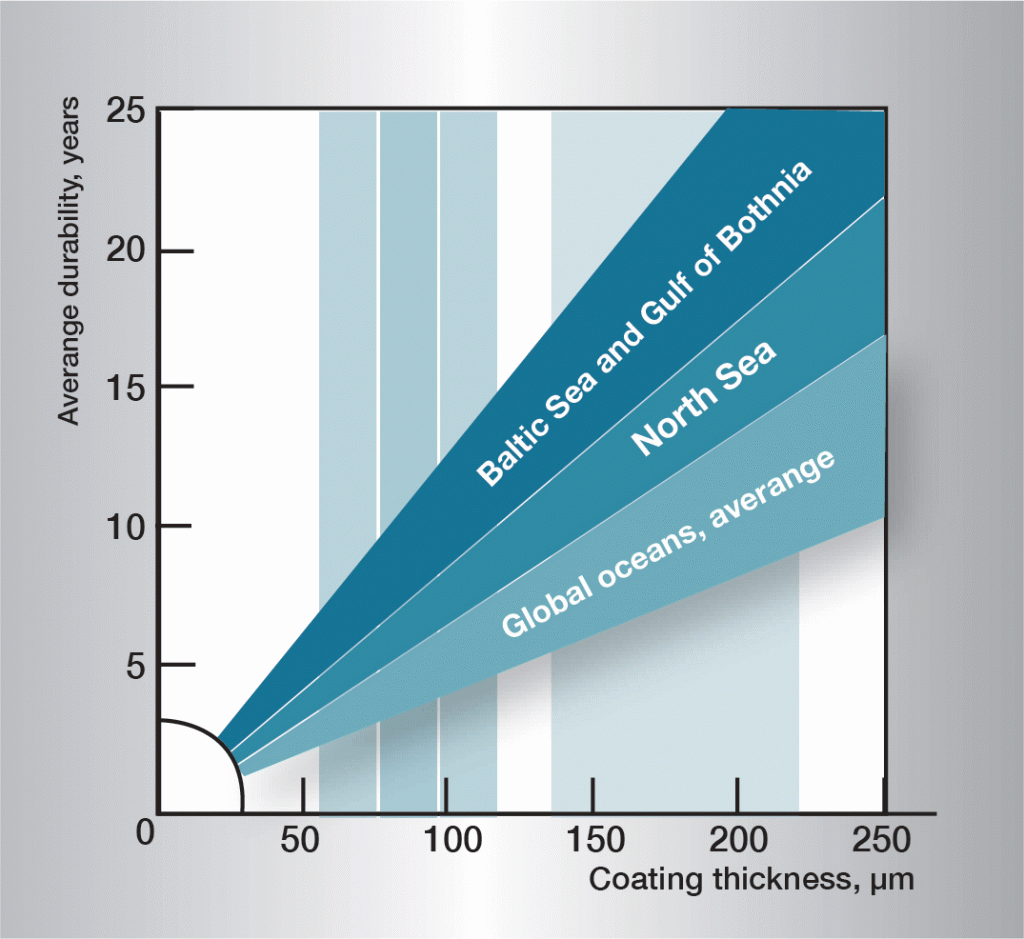
stockage Humide tache
Parfois, un blanc, farineux et volumineux couche appelée de stockage humide tache, ou de la rouille blanche, apparaît sur les surfaces galvanisées (fig.4). La rouille blanche se forme sur les matériaux avec des surfaces brillantes nouvellement galvanisées et en particulier dans les crevasses entre les feuilles étroitement emballées, les cornières et les matériaux similaires. Une condition préalable est que le matériau soit exposé à la condensation ou à l’eau de pluie dans des conditions où l’humidité ne peut pas s’évaporer rapidement., Les surfaces de Zinc qui ont déjà reçu une couche protectrice normale de produits de corrosion sont rarement attaquées. Lorsque les revêtements de zinc sont exposés à l’air, de l’oxyde de zinc et de l’hydroxyde de zinc se forment. Sous l’influence du dioxyde de carbone dans l’air, ceux-ci sont convertis en carbonates de zinc basiques. Si l’accès de l’air à la surface du zinc est limité, comme dans les crevasses étroites, la zone reçoit un manque de dioxyde de carbone pour permettre la formation de la couche normale de carbonates.
la couche de teinture de stockage humide est volumineuse et poreuse et ne se fixe que faiblement à la surface du zinc., En conséquence, la protection contre les attaques continues n’existe pas. La Corrosion peut donc se poursuivre tant que l’humidité reste sur les surfaces. Lorsque la tache de stockage humide s’est produite, l’objet doit être empilé pour permettre aux surfaces de sécher rapidement. Cela arrêtera l’attaque et, avec un accès libre à l’air, la couche protectrice normale sera formée. La tache de stockage humide est progressivement lavée et le revêtement acquiert un aspect normal pour l’acier galvanisé à chaud exposé.,
étant donné que ce produit de corrosion blanc est très volumineux (environ 500 fois celui du zinc à partir duquel il a été formé), il peut sembler grave. Cependant, la tache de stockage humide a souvent peu ou pas d’importance sur la durée de vie de la protection contre la corrosion. Cependant, dans le cas de revêtements très minces, par exemple sur des objets électrolytiques, une attaque sévère de tache de stockage humide peut être importante.
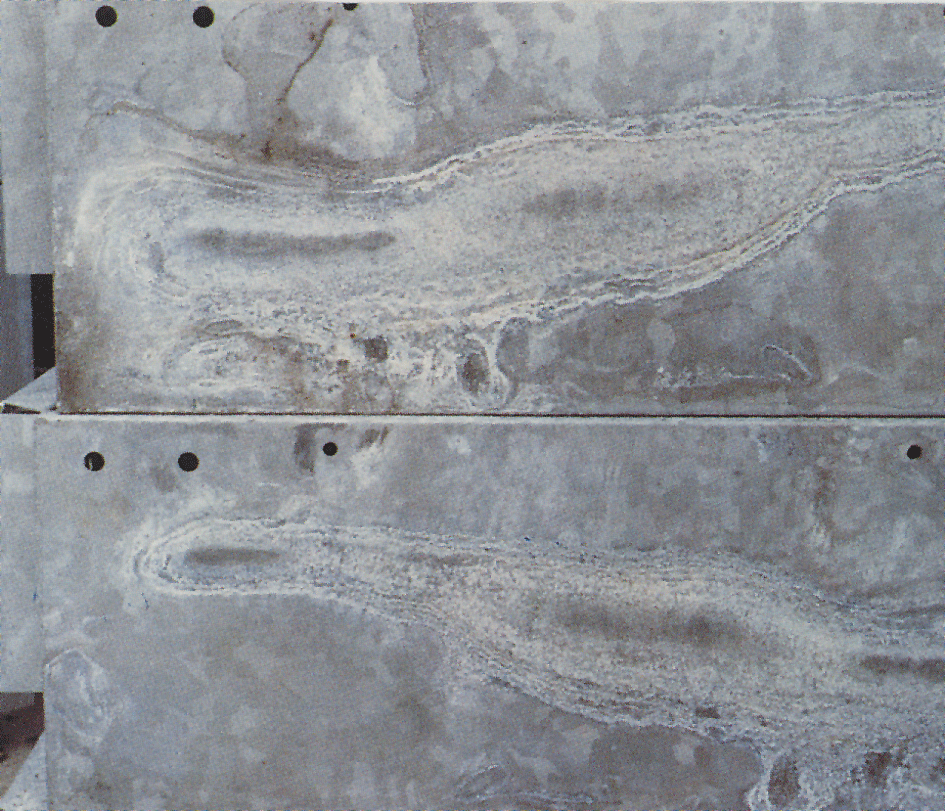
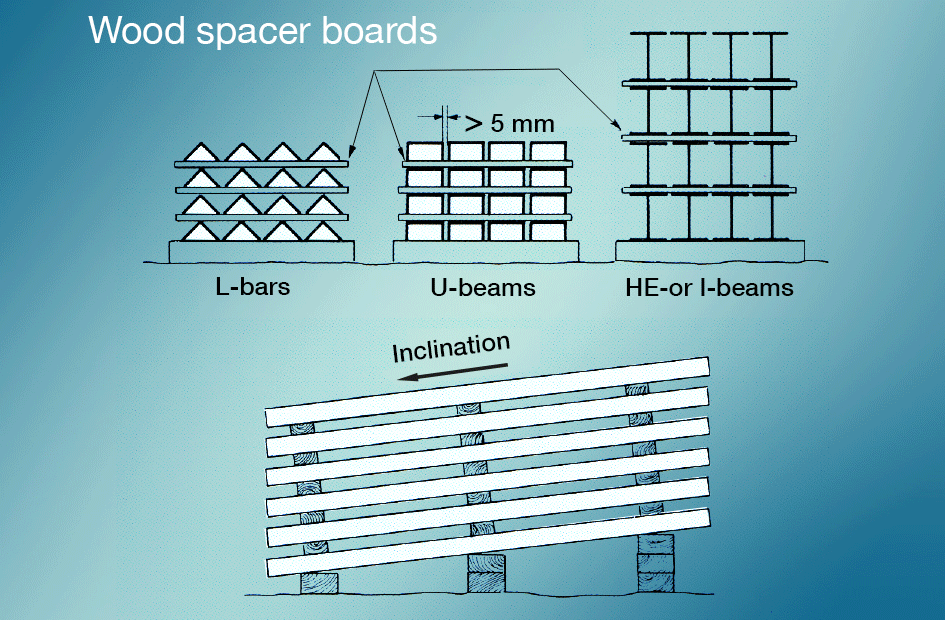
Il est préférable d’éviter les taches de stockage humide en empêchant les surfaces nouvellement galvanisées d’entrer en contact avec la pluie ou les condensats pendant le transport., Les matériaux stockés à l’extérieur doivent être empilés de manière à ce que l’eau puisse s’écouler facilement et que toutes les surfaces soient bien ventilées (fig. 5). La peinture après galvanisation donne une très bonne protection.
Corrosion dans le sol
Les conditions de corrosion dans le sol sont très compliquées et les variations peuvent être importantes entre différents endroits, même ceux qui sont proches les uns des autres. Le sol peut contenir des produits altérés, des sels libres ou liés, des acides et des alcalis, des mélanges de substances organiques, des champignons oxydants ou réducteurs, des micro – organismes, etc., Selon sa structure, le sol a différents degrés de perméabilité à l’air et à l’humidité. Normalement, la teneur en oxygène est inférieure à celle de l’air, tandis que la teneur en dioxyde de carbone est plus élevée.
Les sols suédois ne sont généralement pas très agressifs. La corrosion moyenne du zinc est généralement considérée comme 5 µm par an. Les sols très agressifs sont rarement vus. Dans la Botnie du Nord et de l’ouest, les sols peuvent contenir du soufre. Ils sont souvent noirs, mais s’éclaircissent lorsqu’ils sont exposés à l’air. Dans ces sols, les taux de corrosion du zinc sont très élevés.
Une méthode de détermination de la corrosivité d’un sol consiste à mesurer sa résistivité., Si la resitivité du sol ne peut pas être déterminée, les règles empiriques énumérées à la figure 6 peuvent donner une mesure d’orientation. En ce qui concerne l’exposition des métaux au sol, il est toutefois conseillé de demander l’avis d’experts auprès de sources dûment qualifiées.
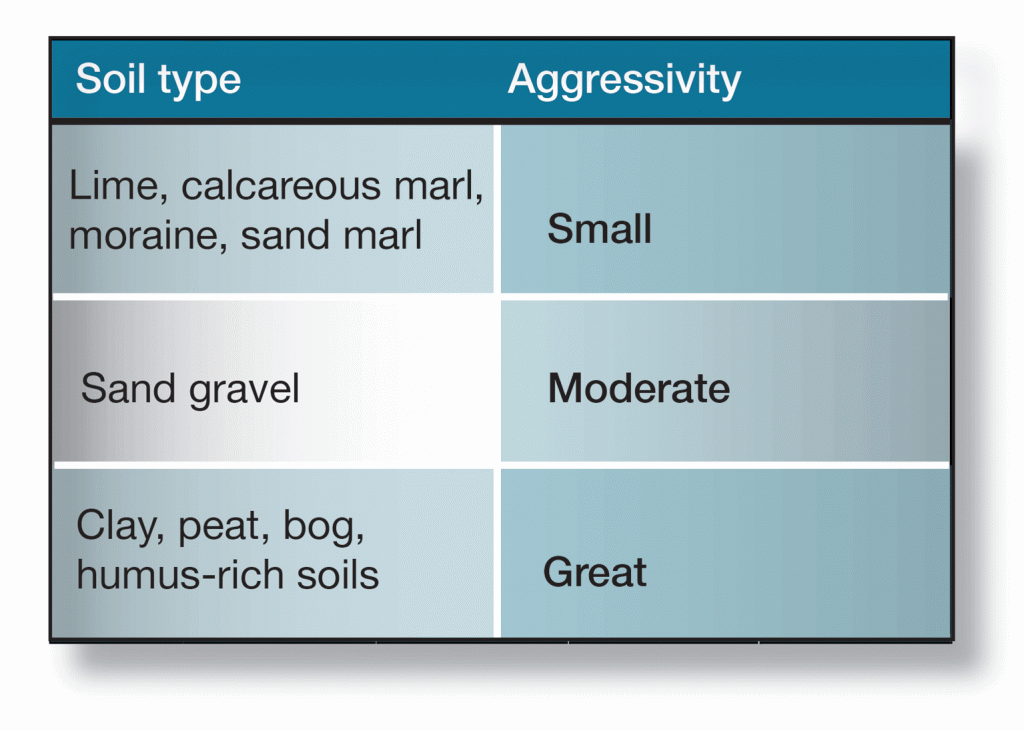
la corrosion Galvanique
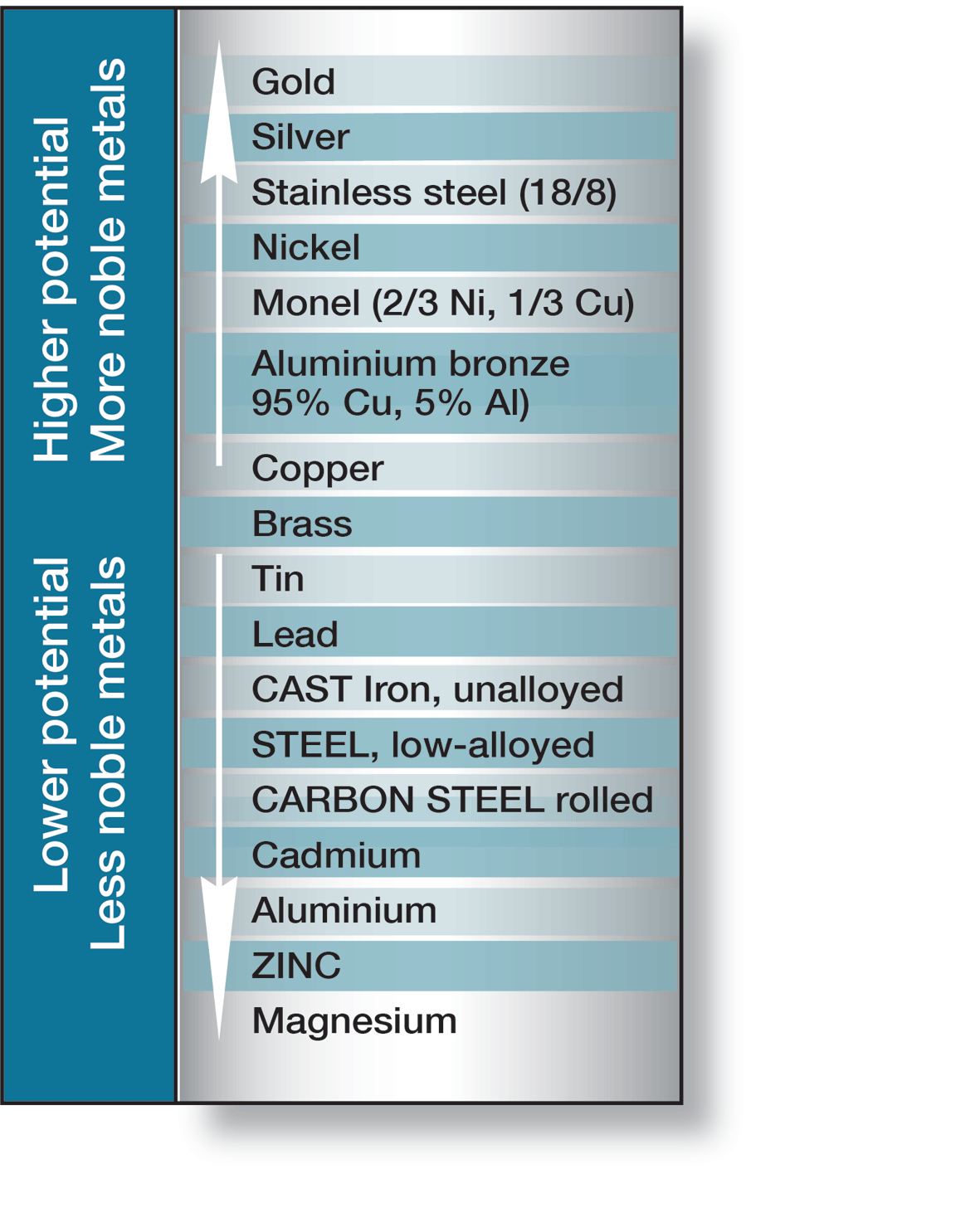
Si deux métaux ou alliages différents, complètement ou partiellement entourés d’un électrolyte, sont connectés, une cellule galvanique est créée. Quel métal devient l’anode ou la cathode est déterminé par leurs potentiels d’électrode dans l’électrolyte en question. Dans l’eau de mer, qui correspond à la majorité des conditions pratiques, certains métaux et alliages prennent des positions différentes à l’échelle électrochimique, illustrée à la figure 7.,
Si l’acier est relié au cuivre ou au laiton, l’acier devient l’anode dans la cellule et se corrode. Cependant, si l’acier est relié au cadmium, à l’aluminium, au zinc ou au magnésium, il devient la cathode et est protégé contre la corrosion, tandis que le métal de l’anode est consommé. La corrosion galvanique est également appelée corrosion bimétallique et est utilisée pour protéger les structures sous-marines de la corrosion, lorsqu’elle est appelée protection cathodique.
protection cathodique offerte par les revêtements de zinc
dans l’acier galvanisé à chaud, le zinc et l’acier sont en bon contact électrique les uns avec les autres., Si le revêtement de zinc est endommagé en présence d’un électrolyte, une cellule galvanique est créée. L’électrolyte pourrait être du condensat ou de l’eau de pluie. Parfois, toute la structure peut être immergée dans un liquide. Dans cette cellule le zinc devient l’anode ou pôle de dissolution, l’acier exposé devient la cathode et est donc protégé de la corrosion.
dans la phase initiale, il est souvent possible de voir une faible formation d’ust sur la partie exposée de la surface en acier où le revêtement a été endommagé, mais après un certain temps, des zones gris blanchâtre se forment qui s’étendent progressivement sur toute la zone endommagée., Le revêtement de zinc corrode et les alliages de zinc peu solubles descendent à la surface de la cathode où ils protègent l’acier contre les attaques continues de rouille. Ceci est souvent appelé « auto-guérison », ce qui est quelque chose d’un mauvais nom puisque la couche de zinc n’est, bien sûr, pas restaurée.
en raison de la protection cathodique générée par le zinc, la rouille ne peut pas « s’infiltrer” sous le revêtement au point d’endommagement de la même manière qu’elle peut s’infiltrer sous des films de peinture ou des revêtements de métaux plus nobles que l’acier., Les revêtements de Zinc sur l’acier sont inhabituels, car une assez grande surface de dommages au revêtement ne provoque pas de perte catastrophique de protection contre la rouille. La gamme de protection cathodique dépend de la nature de l’électrolyte qui crée de la cellule. Pour les structures en atmosphère normale, il est habituel de s’attendre à une action protectrice sur plusieurs millimètres. Cependant, dans l’eau de mer, on peut s’attendre à des distances beaucoup plus grandes.
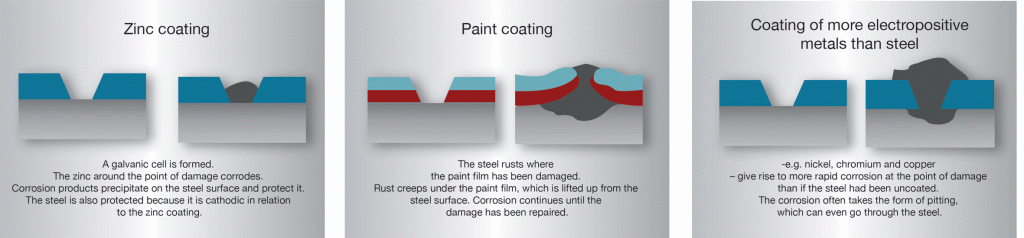
revêtements de Zinc en contact avec des métaux non ferreux
l’échelle de potentiel électrochimique montre que le zinc est moins noble que la plupart des métaux communs. Cela signifie que lorsque le zinc est connecté à ces métaux dans une cellule galvanique, c’est le zinc qui devient la dissolution du pôle. En principe, de telles connexions doivent donc être évitées lorsque cela est possible. Une bonne méthode consiste à utiliser un isolant tel que du plastique ou du caoutchouc au niveau du joint.,
L’Aluminium et l’acier inoxydable peuvent souvent être connectés directement au matériau galvanisé dans l’air ou dans des environnements assez secs sans corrosion notable. Cependant, dans l’eau un isolant doit toujours être utilisée.
Le cuivre et les alliages de cuivre sont plus actifs électriquement et il y a souvent une libération d’ions de cuivre qui se propagent sur de grandes surfaces et provoquent une attaque notable. Pour cette raison, ces métaux ne doivent jamais entrer en contact avec l’acier galvanisé et un isolant doit être utilisé.,
acier galvanisé à chaud en contact avec le mortier, le plâtre et le bois
Le mortier humide et le plâtre attaquent le zinc. L’attaque cesse lorsque le matériau se dessèche. Le bois sec ou modérément humide, à la fois imprégné et non imprégné, peut être cloué avec des clous galvanisés à chaud pour un bon effet. Cependant, dans le cas de clous ou de raccords filetés constamment exposés à l’eau, un matériau résistant aux acides est préféré. D’autres matériaux de construction secs, tels que la laine minérale, n’attaquent pas le zinc.,
Emballage et transport de l’acier galvanisé
même si un revêtement galvanisé à chaud est capable de résister à un traitement assez rugueux, il doit être manipulé avec soin pendant le stockage et le transport. En cas de marchandises longues, l’emballage simple et la liaison en paquets protègent non seulement contre les dommages mécaniques, mais facilitent souvent le transport lui-même. Cependant, l’emballage et la reliure doivent être faits de manière à éviter le risque de contrainte de stockage humide. Des entretoises doivent être utilisées pour prévenir de telles attaques.