El acero es el material más común en uso hoy en día. Sin embargo, el acero tiene una gran desventaja: su alta tasa de corrosión. Por lo tanto, la protección de las estructuras y componentes de acero reviste una gran importancia económica.
la mejor protección anticorrosiva para el acero se obtiene con zinc. Los recubrimientos de Zinc sobre acero protegen contra la corrosión de dos maneras:
- por un efecto barrera, es decir, evitan que el oxígeno y la humedad lleguen a la superficie del acero.,
- dando la protección catódica en rasguños, virutas, bordes etc.
El Zinc es un metal con un potencial galvánico relativamente bajo y una alta tendencia a la corrosión. Sin embargo, la tasa de corrosión es baja en la mayoría de los entornos, ya que la superficie del recubrimiento se cubre rápidamente con productos de corrosión, que posteriormente protegen contra la corrosión adicional.
corrosión en la atmósfera
Cuando un objeto galvanizado en caliente sale del baño de zinc, la superficie del objeto es atacada inmediatamente por el oxígeno en el aire., La capa de óxido resultante tiene muy poca capacidad para proteger contra la corrosión. Sin embargo, el agua y el dióxido de carbono en el aire cambian rápidamente la capa de óxido a carbonatos de zinc. Estos dan una capa sellada con muy buena adherencia. Dado que los carbonatos tienen una solubilidad muy baja en agua, brindan una excelente protección a la superficie del recubrimiento de zinc. La superficie original brillante con un lustre metálico desaparece para ser reemplazada por un color gris claro mate (fig.1).
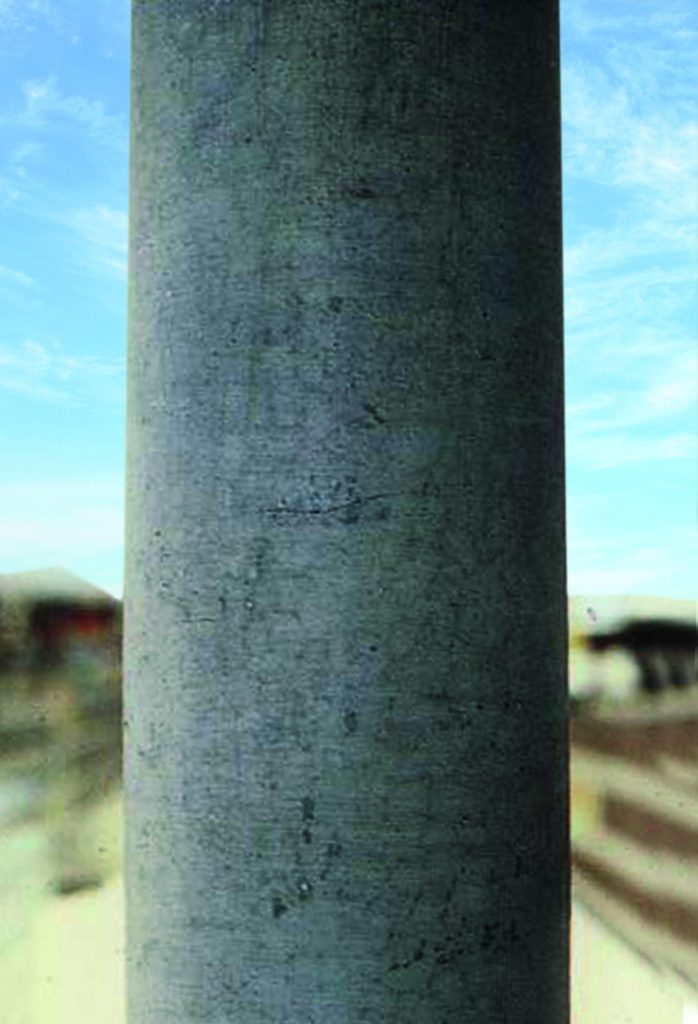
la figura 1., Superficie expuesta de un recubrimiento de zinc con capa exterior de zinc puro. La superficie brillante desaparece para ser reemplazada por productos de corrosión gris (a veces llamados pátina de zinc).
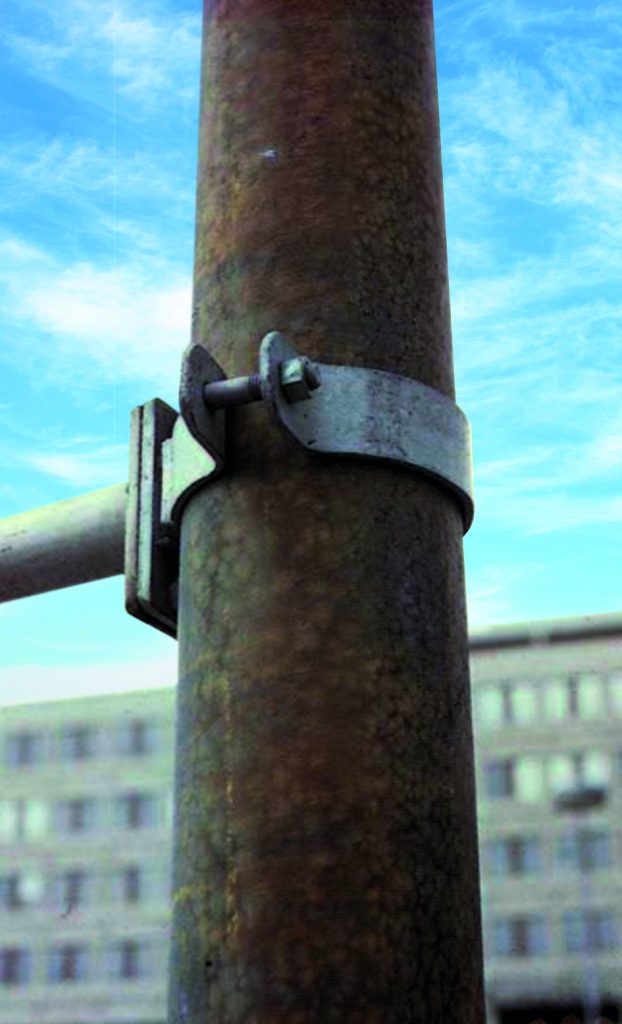
Fig. 2. Superficie descolorida en la columna de iluminación. El recubrimiento consiste principalmente en una aleación de hierro y zinc que se extiende a la superficie. El hierro está expuesto durante la corrosión, lo que conduce a la formación de óxido. Es solo óxido superficial y es solo de importancia estética.,
El aire exterior contiene mayor o menor cantidad de elementos corrosivos: gases, hollín, humedad (niebla, rocío, lluvia, nieve), polvo inerte y agresivo. Los niveles pueden variar con la ubicación y la época del año. Los sulfatos y sulfitos de zinc son solubles en agua y tienen una mala adhesión a la superficie de zinc. Por lo tanto, son arrastrados fácilmente por la lluvia. Una superficie fresca de zinc se expone entonces al ataque del oxígeno en el aire y se repite el ciclo de corrosión. Por lo tanto, la corrosión en el aire que contiene óxidos de azufre es mayor que en el aire limpio., Sin embargo, la cantidad de dióxido de azufre en la atmósfera ha disminuido drásticamente en los últimos años y, en consecuencia, la corrosión del zinc también ha disminuido.
En ambientes marinos, la corrosión del zinc está influenciada por el contenido de sal del aire. Sin embargo, el aire marino contiene pequeñas cantidades de sales de magnesio, con buenas influencias pasivantes. Por lo tanto, la corrosión no es tan grande como cabría esperar. El contenido de sal del aire se reduce rápidamente lejos de la costa.
la corrosión del zinc está influenciada por muchos factores., Esto significa que no se puede dar una fórmula de aplicación general para las tasas de corrosión. Sin embargo, los recubrimientos de Zinc se han utilizado durante mucho tiempo, en una amplia gama de condiciones, para proteger el acero del óxido. También se ha realizado un gran número de pruebas a largo plazo. Por lo tanto, el conocimiento sobre la corrosión del zinc y las tasas de corrosión en diferentes entornos es bueno. Hoy en día, hay ejemplos de recubrimientos de zinc que han estado expuestos durante más de cien años.
El color de los productos de corrosión varía según el entorno en el que se forman., Los entornos marinos ofrecen productos de corrosión algo más blancos en comparación con los entornos rurales y urbanos. Los productos de corrosión suelen ser más oscuros en entornos urbanos.
corrosión en líquidos
la superficie de zinc generalmente se cubre con una capa protectora de productos de corrosión cuando se sumerge en un líquido. Sin embargo, los líquidos pueden ser ácidos o alcalinos y pueden contener partículas disueltas o sólidas de sustancias agresivas. La temperatura y el caudal del líquido también son importantes., Todo esto significa que la capa protectora puede tener una composición muy variable o puede no formarse en absoluto.
la corrosión electroquímica, que desempeña un papel subordinado en el aire, es de mayor importancia en los líquidos. El grado de corrosión electroquímica depende de la conductividad eléctrica del líquido, que afecta la influencia protectora de la capa de zinc sobre áreas mayores o menores.
el valor de pH del líquido es de mayor importancia. La tasa de corrosión del zinc es normalmente baja y estable en el rango de pH de 5,5-12,5, a temperaturas entre 0 y 20 °C., La corrosión fuera de este rango suele ser más rápida.
El agua dura, que contiene cal y magnesio, es menos agresiva que el agua blanda. Junto con el dióxido de carbono, estas sustancias forman carbonatos escasamente solubles en la superficie del zinc, protegiendo al zinc contra una mayor corrosión.
El agua blanda a menudo ataca el zinc, ya que la ausencia de sales significa que no se puede formar la capa protectora.
Las aguas blandas agresivas se pueden encontrar en muchos ríos y lagos de Finlandia, Noruega, Suecia y entornos similares.
Si el caudal es mayor que 0.,5 m / s se inhibe la formación de la capa protectora sobre la superficie de zinc y se acelera la corrosión.
La temperatura del agua es de gran importancia para la tasa de corrosión. Por encima de aproximadamente 55 ° C, los productos de corrosión que forman capas adquieren una estructura de grano grueso y pierden adherencia a la superficie de zinc. Se desprenden fácilmente y exponen zinc nuevo y fresco para un ataque de corrosión continuo y rápido. La velocidad de corrosión alcanza un máximo a unos 70 ° C, después de lo cual disminuye de modo que a 100 °C es aproximadamente la misma que a 50 °C.,
la secuencia de corrosión en el agua es muy compleja y está fuertemente influenciada por variaciones muy pequeñas en la composición del agua. Por lo tanto, es difícil establecer normas de aplicación general. La información de la figura 3 se basa en la experiencia práctica y da directrices para algunos tipos diferentes de agua.
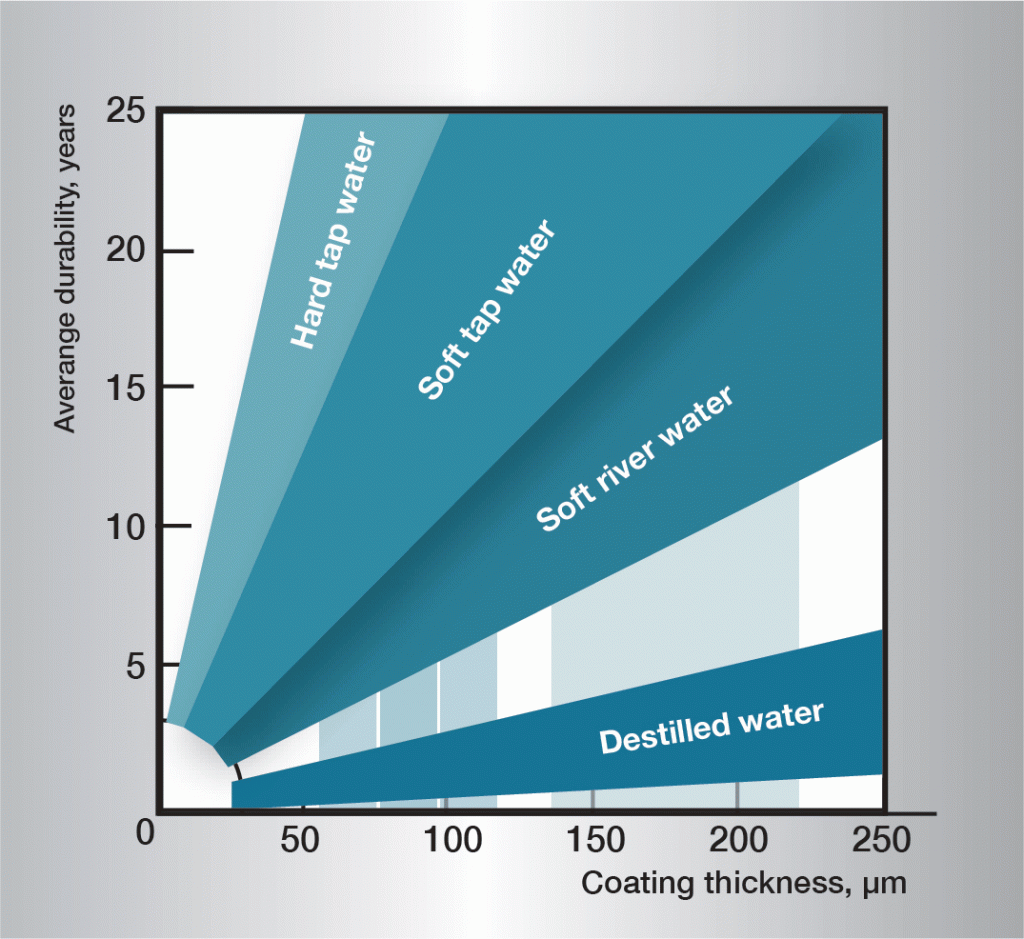
Fig. 3. Vida útil en diferentes aguas.,
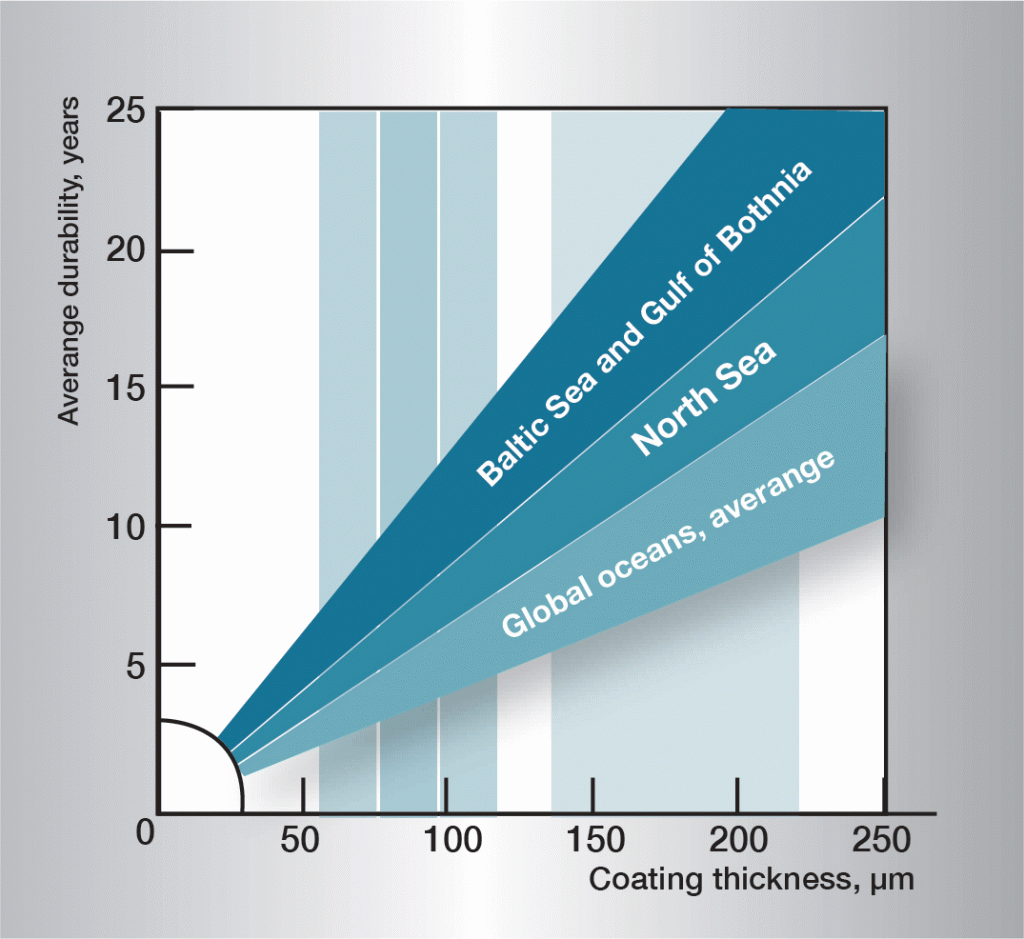
mancha de almacenamiento húmedo
a veces una capa blanca, harinosa y voluminosa llamada mancha de almacenamiento húmedo, o óxido blanco, aparece en superficies galvanizadas (fig.4). El óxido blanco se forma en materiales con superficies brillantes recién galvanizadas y especialmente en grietas entre láminas muy compactas, hierro angular y materiales similares. Una condición previa es que el material esté expuesto a condensación o agua de lluvia en condiciones donde la humedad no se puede evaporar rápidamente., Las superficies de Zinc que ya han recibido una capa protectora normal de productos de corrosión rara vez son atacadas. Cuando los recubrimientos de zinc se exponen al aire, se forman óxido de zinc e hidróxido de zinc. Bajo la influencia del dióxido de carbono en el aire, Estos se convierten en carbonatos básicos de zinc. Si el acceso de aire a la superficie de zinc está restringido, como en grietas estrechas, entonces el área recibe dióxido de carbono insuficiente para permitir que se forme la capa normal de carbonatos.
la capa de tinción de almacenamiento húmedo es voluminosa y porosa y solo se adhiere libremente a la superficie de zinc., Como resultado, no existe protección contra ataques continuos. Por lo tanto, la corrosión puede continuar mientras la humedad permanezca en las superficies. Cuando se ha producido una mancha de almacenamiento húmedo, el objeto debe apilarse para permitir que las superficies se sequen rápidamente. Esto detendrá el ataque y, con libre acceso al aire, se formará la capa protectora normal. La mancha de almacenamiento húmedo se lava gradualmente y el recubrimiento adquiere una apariencia normal para el acero galvanizado en caliente expuesto.,
dado que este producto de corrosión blanco es muy voluminoso (aproximadamente 500 veces el del zinc del que se formó), puede parecer grave. Sin embargo, la mancha de almacenamiento húmedo a menudo tiene poca o ninguna importancia en la vida útil de la protección contra la corrosión. Sin embargo, en el caso de recubrimientos muy finos, por ejemplo, en objetos galvanizados, un ataque severo de mancha de almacenamiento húmedo puede ser importante.
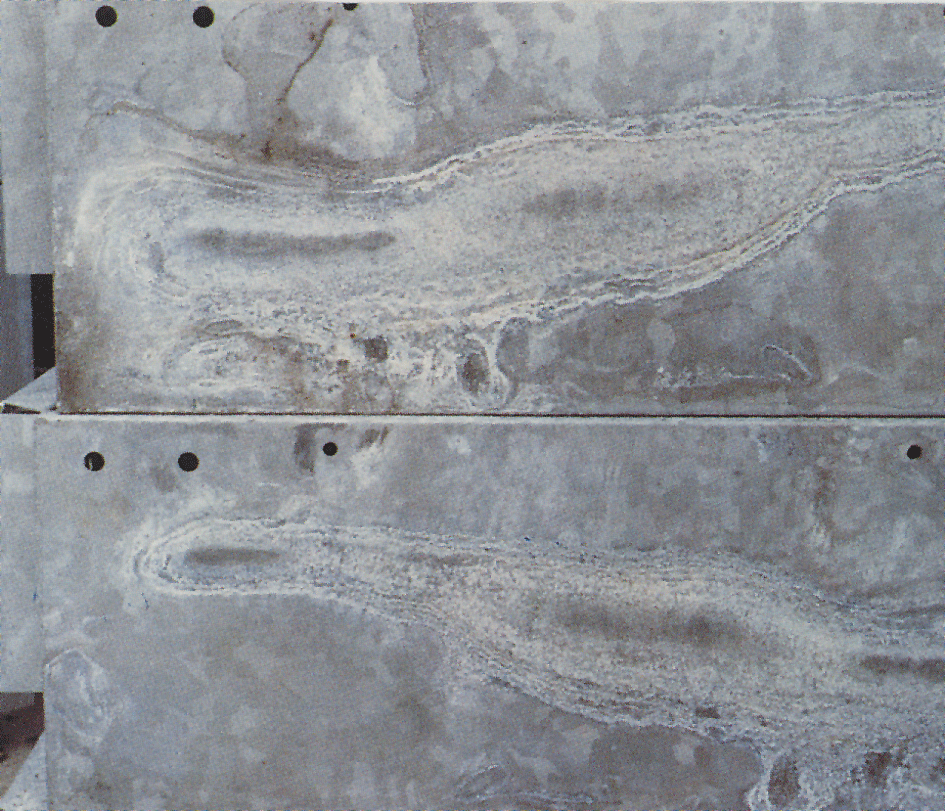
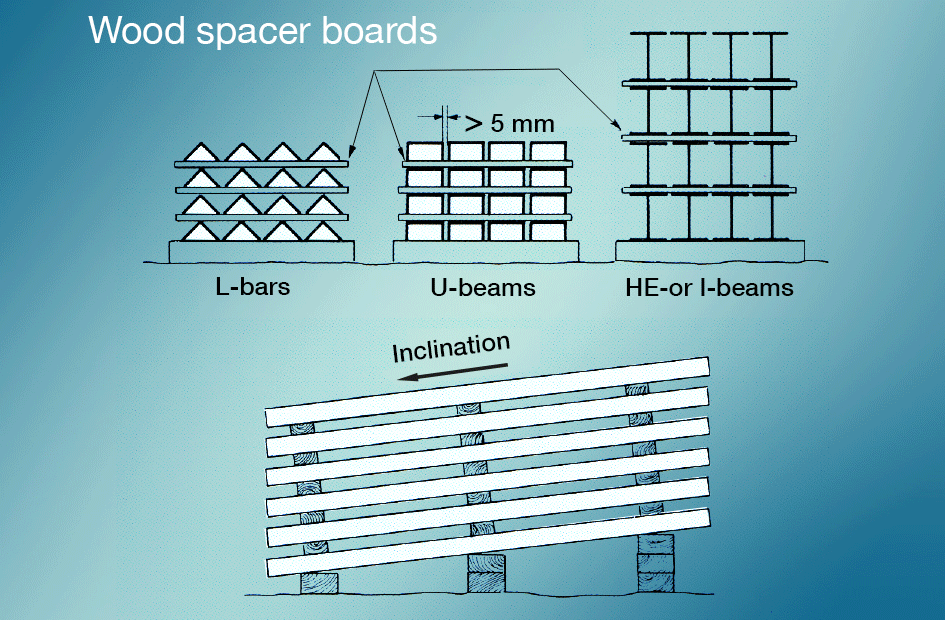
la mejor manera de evitar las manchas de almacenamiento húmedo es evitar que las superficies recién galvanizadas entren en contacto con la lluvia o el condensado durante el transporte., Los materiales almacenados al aire libre deben apilarse para que el agua pueda escurrirse fácilmente y para que todas las superficies estén bien ventiladas (fig. 5). La pintura después de galvanizar da muy buena protección.
corrosión en el suelo
Las condiciones de corrosión en el suelo son muy complicadas y las variaciones pueden ser grandes entre diferentes ubicaciones, incluso las que están muy cerca entre sí. El suelo puede contener productos Erosionados, sales libres o Unidas, ácidos y álcalis, mezclas de sustancias orgánicas, hongos oxidantes o reductores, microorganismos, etc., Dependiendo de su estructura, el suelo tiene diferentes grados de permeabilidad al aire y la humedad. Normalmente, el contenido de oxígeno es menor que en el aire, mientras que el contenido de dióxido de carbono es mayor.
los suelos suecos generalmente no son muy agresivos. La corrosión promedio para el zinc generalmente se toma como 5 µm por año. Rara vez se ven suelos severamente agresivos. En Botnia Norte y oeste, los suelos pueden contener azufre. A menudo son negras, pero se aclaran cuando se exponen al aire. En estos suelos, las tasas de corrosión del zinc son muy altas.un método para determinar la corrosividad de un suelo es medir su resistividad., Si no se puede determinar la resitividad del suelo, las reglas empíricas enumeradas en la figura 6 pueden dar una medida de orientación. Sin embargo, cuando se trata de la exposición de metales al suelo, es aconsejable buscar el asesoramiento de expertos de fuentes debidamente calificadas.
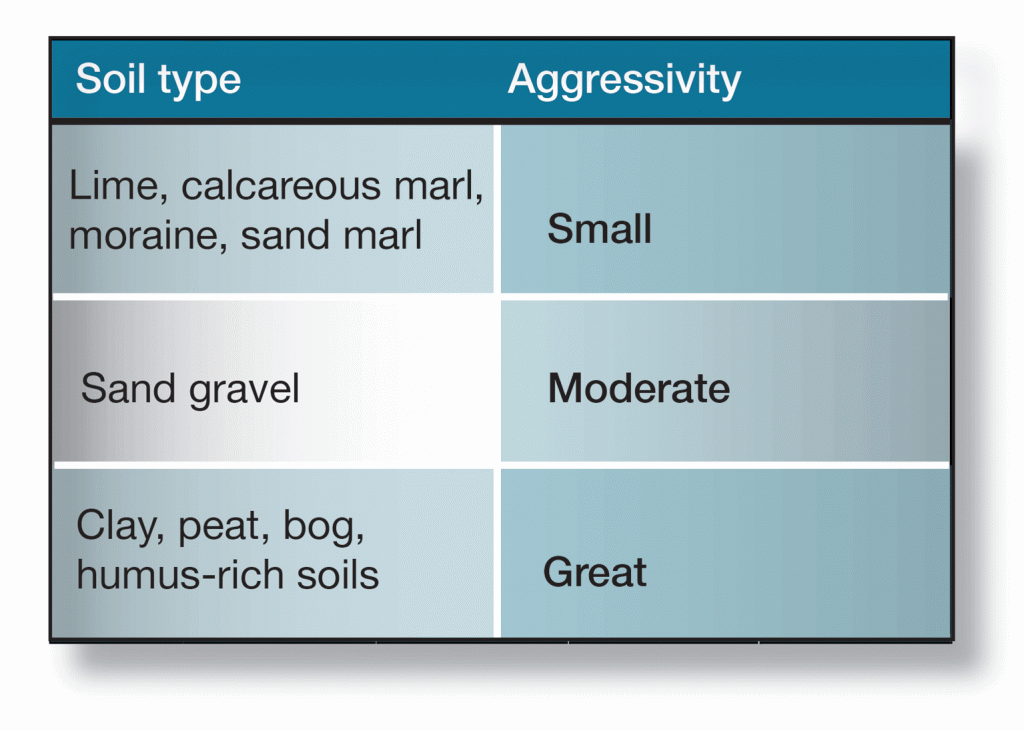
la corrosión Galvánica
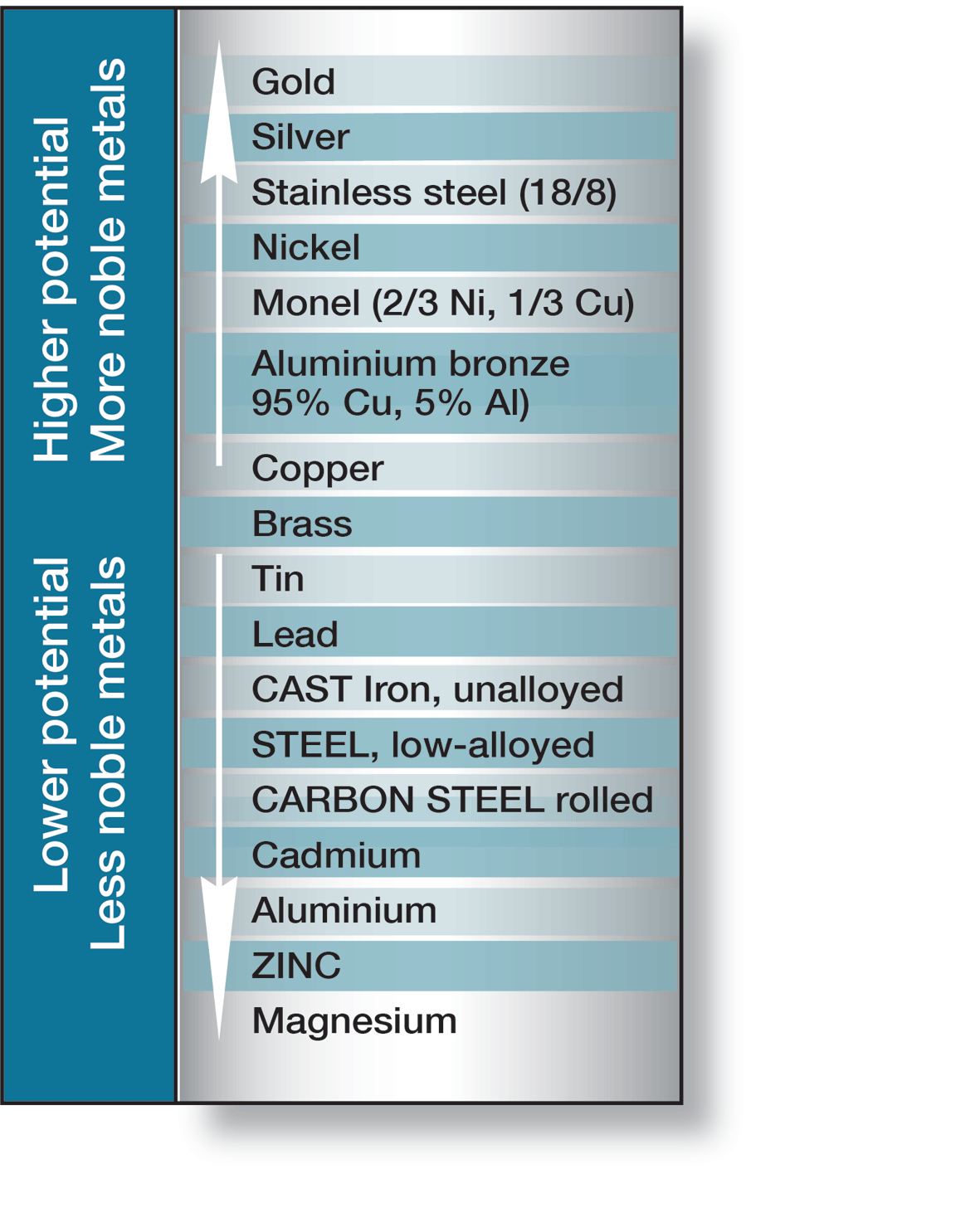
Si se conectan dos metales o aleaciones diferentes, completa o parcialmente rodeados por un electrolito, se crea una celda galvánica. Qué metal se convierte en el ánodo o cátodo está determinado por sus potenciales de electrodo en el electrolito en cuestión. En el agua de mar, que corresponde a la mayoría de las condiciones prácticas, algunos metales y aleaciones ocupan diferentes posiciones en la escala electroquímica, como se muestra en la figura 7.,
si el acero está conectado con cobre o latón, el acero se convierte en el ánodo en la celda y se corroe. Sin embargo, si el acero está conectado al cadmio, aluminio, zinc o magnesio, se convierte en el cátodo y está protegido contra la corrosión, mientras que el ánodo metálico se consume. La corrosión galvánica también se llama corrosión bimetálica y se utiliza para proteger las estructuras submarinas de la corrosión, cuando se denomina Protección Catódica.
Protección Catódica proporcionada por los recubrimientos de zinc
en acero galvanizado en caliente, el zinc y el acero están en buen contacto eléctrico entre sí., Si el recubrimiento de zinc se daña en presencia de un electrolito, se crea una célula galvánica. El electrolito podría ser condensado o agua de lluvia. A veces toda la estructura puede sumergirse en líquido. En esta celda, el zinc se convierte en el ánodo o polo de disolución, el acero expuesto se convierte en el cátodo y, por lo tanto, está protegido de la corrosión.
en la fase inicial a menudo es posible ver una formación ust débil en la parte expuesta de la superficie de acero donde el recubrimiento se ha dañado, pero después de un tiempo se forman áreas blanquecinas y grises que gradualmente se extienden por toda el área dañada., El recubrimiento de zinc se corroe y las aleaciones de zinc escasamente solubles descienden a la superficie del cátodo donde protegen el acero del ataque continuo de óxido. Esto a menudo se llama «auto-curación», que es algo de un nombre inapropiado ya que la capa de zinc, por supuesto, no se restaura.
debido a la protección catódica generada por el zinc, el óxido no puede «arrastrarse» debajo del recubrimiento en el punto de daño de la manera en que puede arrastrarse debajo de películas de pintura o recubrimientos de metales más nobles que el acero., Los recubrimientos de Zinc en el acero son inusuales, ya que un área bastante grande de daño al recubrimiento no causa una pérdida catastrófica de protección contra la oxidación. El rango de protección catódica depende de la naturaleza del electrolito que crea la célula. Para estructuras en atmósferas normales, es habitual esperar una acción protectora de varios milímetros. Sin embargo, en el agua de mar se pueden esperar distancias significativamente mayores.
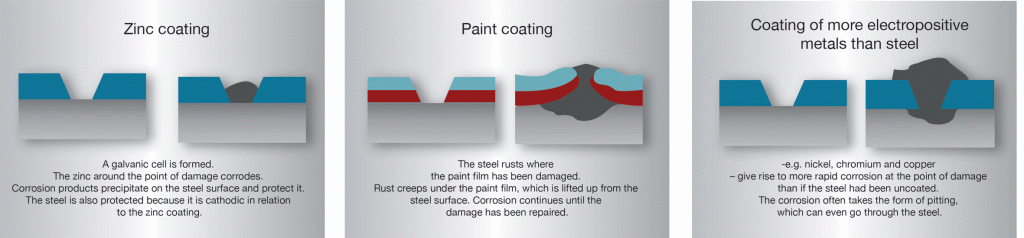
recubrimientos de Zinc en contacto con metales no ferrosos
la escala de potencial electroquímico muestra que el zinc es menos noble que la mayoría de los metales comunes. Esto significa que cuando el zinc está conectado a estos metales en una celda galvánica, es el zinc el que se convierte en el polo de disolución. En principio, por lo tanto, tales conexiones deben evitarse cuando sea posible. Un buen método es usar un aislante como plástico o goma en la articulación.,
El aluminio y el acero inoxidable a menudo se pueden conectar directamente al material galvanizado en entornos de aire o bastante secos sin que se produzca una corrosión notable. Sin embargo, en el agua siempre se debe usar un aislante.
El Cobre y las aleaciones de cobre son más eléctricamente activas y a menudo hay una liberación de iones de cobre que se extienden sobre grandes superficies y causan un ataque notable. Por esta razón, nunca se debe permitir que estos metales entren en contacto con el acero galvanizado y se debe usar un aislante.,
acero galvanizado en caliente en contacto con mortero, yeso y madera
mortero húmedo y zinc de ataque de yeso. El ataque cesa cuando el material se seca. La madera seca o moderadamente húmeda, tanto impregnada como no impregnada, se puede clavar con clavos galvanizados en baño caliente con buen efecto. Sin embargo, en el caso de clavos o uniones roscadas que están constantemente expuestas al agua, se prefiere un material resistente a los ácidos. Otros materiales de construcción secos, como la lana mineral, no atacan al zinc.,
Embalaje y transporte de acero galvanizado
aunque un recubrimiento galvanizado en caliente es capaz de soportar un tratamiento bastante áspero, debe manejarse con cuidado durante el almacenamiento y el transporte. En el caso de mercancías largas, el simple embalaje y encuadernación en paquetes no solo protege contra daños mecánicos, sino que a menudo facilita el transporte en sí. Sin embargo, el embalaje y la encuadernación deben hacerse de tal manera que se evite el riesgo de tensión de almacenamiento húmedo. Deben utilizarse espaciadores para prevenir esos ataques.